フォーミュラEシーズン5 2018/2019
Automobile study
フォーミュラEに参戦するヴェンチューリチームとHWAチームにパワートレーンを供給するZFが、投入する技術に関するワークショップを開催した。そこで明かされた最先端技術を覗いみてみよう。
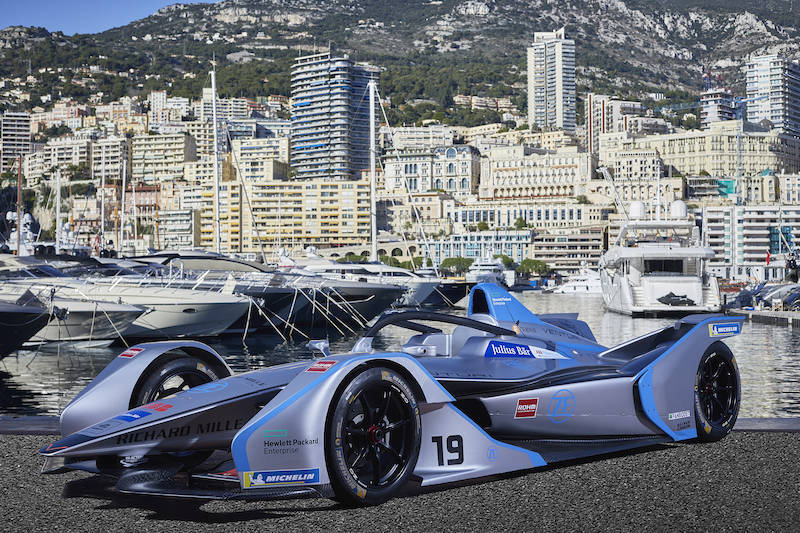
競争領域で差をつけるために
フォーミュラEは100%電動モーターで走る電気自動車で、レギュレーションにより共通パーツが多く存在する。別な言い方をすると共通パーツ以外が競争領域というわけで、その中心となるのがモーター、パワーエレクト二クス(インバーター)、減速機でバッテリーは共通化されている。
ZFのワークショップではそのパワーエレクトロニクスについての説明があった。バッテリーはリチウムイオンバッテリーが採用されているが、これは直流しか蓄電も出力できない。しかし、モーターは交流でしか作動しないため、その変換(DC-AC)が必要になる。またモーターによる回生エネルギーは交流で発電されるため、バッテリーに蓄電するには、ここでも直流への変換が必要になる。その変換をしているのがパワーエレクト二クスだ。
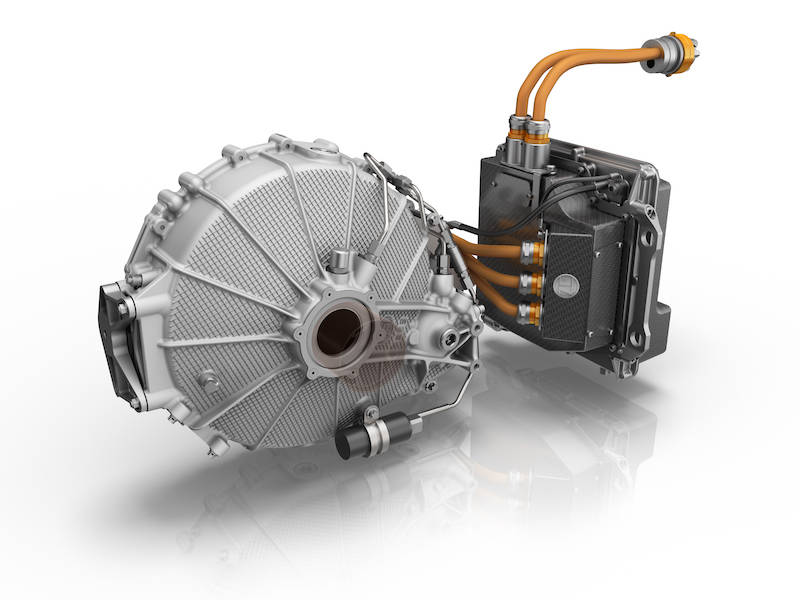
このパワーエレクトロ二クスは、常に両方向の変換を行なっているため、変換、出力ロスなどの効率を高めることが重要になる。その効率の鍵を握るのが「絶縁ゲート型バイポーラトランジスター:IGBT」と呼ばれる半導体で、各半導体メーカーが研究・開発を行なっている。ZFでは、これまでクルマには使われてこなかった半導体、SiCというシリコンカーバイドを投入したのだ。このことにより、高効率なパワートレーンになっている。
SiCシリコンカーバイドによる高効率化
半導体は電気の流れの遮断、通電をするパーツで、静止状態には電気を遮断し、電圧をかけるか電界をつくることで電気を流す役目をしている。特にクルマに使用するモーターは三相交流の電流の流れがあり、U、V、W相の電流の流し方で、モーターの出力など特性をコントロールしている。その三相をコントロールするのがIGBT(絶縁ゲート型バイポーラトランジスタ)と呼ばれる半導体スイッチング素子で、通常はシリコンが使われている。
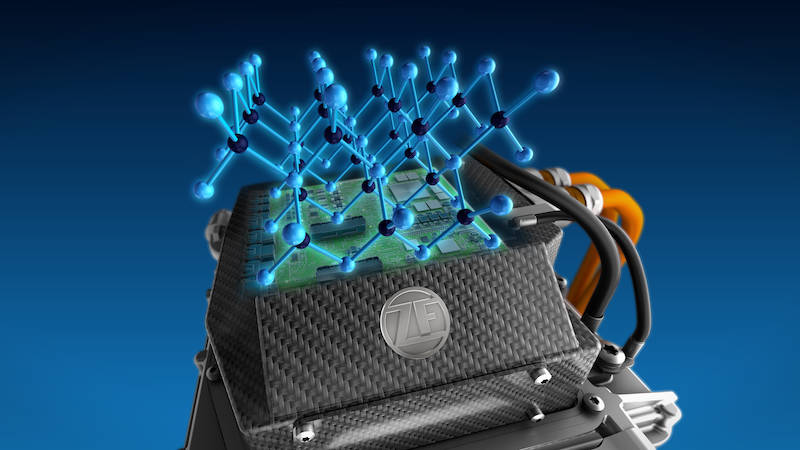
ZFでは、ベンチューリやHWAに供給するこの半導体をSiCパワー半導体にして高効率化しているというわけだ。シリコンに対してこのSiCでは高耐圧で10倍、高耐熱で1000度、小型化で1/1000、速度で100MHzの差があるという。
出力する時に瞬間的に高電圧で電流を流すと、この半導体が耐えられる電圧は半導体の厚みに比例し、高電圧になれば厚みが増す。SiCはシリコンに対して10倍の耐圧性があるというから、薄く小型化ができるというわけだ。しかも熱に強いという特性もある。ただし、発熱している時点で効率を落としているので、熱を出さない研究も進められている。
そして速度というポイントでは、バッテリーに蓄えられたエネルギーは、質量ゼロの素粒子である電子でできているが、その電子はアインシュタインの相対性理論では光速で動くという理屈。もちろんケーブルなどの内部抵抗で速度は落ちるものの、液体燃料やガス燃料より高速で移動するわけで、モーターの出力が低回転から出力できる理由がここにある。つまり、SiCは電子の移動速度の点でもシリコンよりも優れているというわけだ。
これは従来の半導体の1/10の薄さで同じ電圧が処理できることを意味している。ZFでパワーエレクトロニクスの研究をしているマルコ・デング博士によると1cmあたり3メガボルトの電圧まで耐えられるという。これまで電気自動車のモーターは400Vで駆動していたが2019年には800Vの電気自動車が発売される見込みともいう。デング博士によると2倍の電圧にするのは、充電時間を短縮するためで、400km走行するための充電時間は15分から20分になる、と説明している。
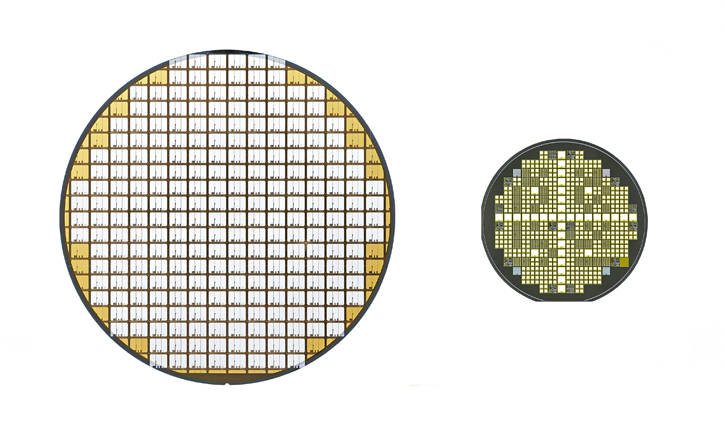
つまり、シリコンカーバイドを採用することで、さまざまな効率をあげることができるため、たとえば同じバッテリーサイズであれば、航続距離を10%伸ばすことができ、あるいはバッテリーを小型化することも可能になる。
このことはSiCの価格にも絡む問題で、現在はシリコンに比較して10倍の値段がする。この価格をZFではシステム全体で吸収できるように考えているのだ。それは、効率が良くなった分、バッテリーの小型化ができつつ、従来の航続距離も確保できる。高耐熱性のため冷却システムがコンパクトに、かつ冷却能力も抑えたもので十分になる。そしてなによりもパワーエレクトロニクス本体の小型化が可能となり、全体の質量も軽量化され、エネルギー損出量も減るといったプラスのスパイラル構造で打ち消していく戦略だ。
ZFではこのパワーエレクトロニクスであるシリコンカーバイドのパワー半導体を、乗用車用の量産に向けて開発している。上記のようなシステムとしての提供となるだろうが3年から4年後あたりを目安に量産化をする予定ということだ。
ZFがフォーミュラEに参戦するわけ
こうした開発はフォーミュラEに参戦したからこそ、可能になったとZFでは説明している。ZFは、シーズン4まではベンチューリにはパワーエレクトロ二クスの供給を行なっていなかった。そのため、シーズン5ではチームからスペックを提供してもらい、どのようなパワートレーンが必要になるか検討することから始まった。
いくつかのコンセプトを作り、シミュレーションをし、最大出力とどういうロスが出るかの検証。出力カーブとロスをそれぞれ分析し、どのように優れているのか、いないのかを検証するなど多角的に検討し、採用するコンセプトを絞った。
もっとも重要と考えたことは、パワートレーンの効率の良さを重視したということだ。次に重要視したのが質量である。そして3つ目の評価は加速性能で0-100km/hを何秒で加速できるかという数値だった。一方でトランスミッションでも3つのアイディアがあり、シングルギヤと2速タイプのコンセプトを2モデル用意した。2速タイプはギヤレシオなどのパラメータ違いだという。そして検証の結果、シングルタイプをチョイスしたわけだ。
また、効率と軽量化が重要ポイントとしたが、イナーシャ(回転慣性)の点でも注力している。イナーシャをいかに抑えるかが効率を上げるポイントにもなるからだ。その回答は3つあり、モーターとギヤボックスをコンパクトに作ること。そしてタイヤが伝えられる最大トルクにギヤ比を最適化すること、そして回転部品の軽量化という3点だという。
シングルスピードのギヤボックス、インバーターのハウジングはカーボン、ギヤボックスは軽量合金を採用し、シーズン4と比較し、このモーター、インバーター、ギヤボックスのコンポーネンツで20%の軽量化ができたという。これらの軽量化によりイナーシャの軽減をし、さらにパワー密度では35%増加させることができている。
こうした製品づくりにおいてはZFがこれまで培った量産技術を活かし、また、カーボン、軽量合金などの新素材技術の活用、3Dプリンターなどでのラピットプロトタイピング(迅速な試作)などの生産技術を磨くことにもなったという。
一方で、レースという環境はダメージを受ける環境、体験ができるわけで、しかも高度な要求があり、高精度なレンジ測定が必要とされ、迅速な対応というものが求められる。したがってベストプラックティスの蓄積だとも言っている。そのひとつがシリコンカーバイドや銅線を巻く技術であったりにつながっているというわけだ。
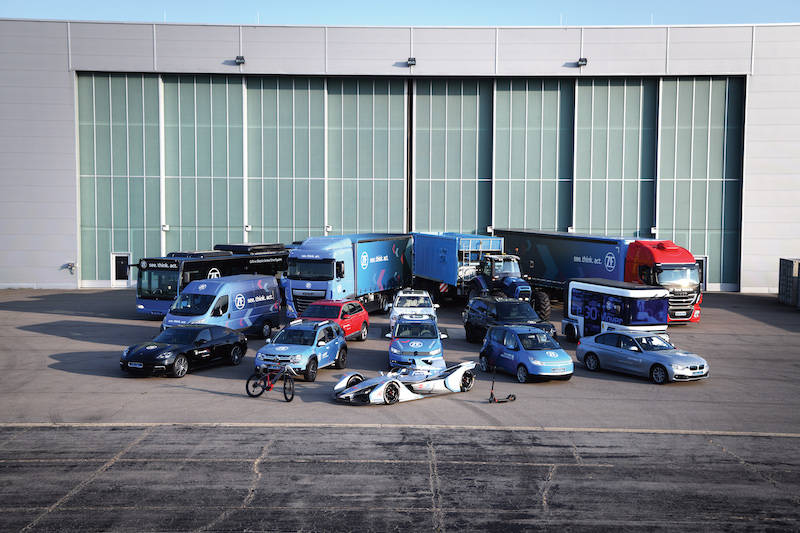
こうしたさまざまなことの限界がわかるのもレースというフィールドだからであり、フォーミュラEのテクノロジー、プロセス、スタッフのマインドセットのレベルアップなどが可能になったという。<レポート:高橋明/Akira Takahashi>
【関連記事】
【トヨタ】電力損失を低減する新素材の高効率パワー半導体を採用したPCUを開発
トヨタ さらに燃費向上 次世代のハイブリッド技術 SiCパワー半導体インバーター搭載車の公道試験開始