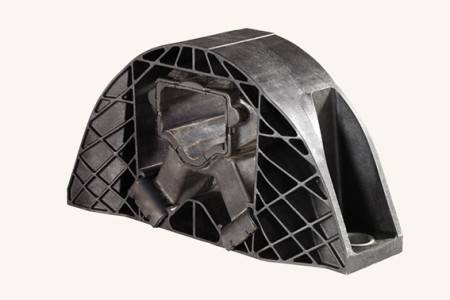
2013年3月21日、ZFはルノー、日産が製造する小型乗用車、電気自動車に軽量プラスチック製のエンジンマウントの供給を開始すると発表した。最新のプラスチック製エンジンマウントは優れた性能と、既存のゴム/金属を接合したエンジンマウントに比べて約25%の重量軽減を実現しているという。
現在は燃費、CO2排出量の低減を目指すために軽量化設計がキーテクノロジーとなっているが、そのためにクルマを構成する個々の部品を軽量化するという取り組みは欠かすことはできない。ZFフリードリヒスハーフェン社は、世界に先駆けてプラスチック製のフレームにゴムを接合した構造のエンジンマウントを開発。この新製品が、ルノー・日産グループに採用された。このエンジンマウントは従来の金属のフレームにゴムを接合した構造とまったく同様に振動を減衰する機能を実現しつつ、重量は約25%も削減されるのだ。
この新しいプラスチック製エンジンマウントの量産は始まったばかりだが、ルノー・日産グループが生産するベーシックカーからコンパクトカーまでの小型車6モデルの一部仕向け地モデル、日産アルメーラ(ラティオの海外生産モデル)やルノーの電気自動車「ZOE(ゾエ)」に採用されている。
このエンジンマウントは、特別な製法で作られたプラスチック製の外郭部、その内側に接合されたゴム、そしてブラケットというエンジンマウントを構成する要素を組み合わせたものだ。
「我々が目指したのは、一般的なエンジンマウントを軽量化する最大の可能性を具現化し、その機能と信頼性の両方を最適化することでした」とシャシーテクノロジー事業部の防振ゴム部門の責任者であるトーステン・ブレマー博士は語る。従来はアルミニウムの一体鋳造で作られていたエンジンマウントの外郭部分を、ガラス繊維を混入して強化したポリアミド(FRM)樹脂に置き替えたのだ。部品全体の重量が25%削減されたのは、このプラスチック製外郭部分による効果だ。もちろんこれが実用化されるためには、既存品と同等の機能と安定度、耐久性を備えている必要があり、さらにこの部分はまったく腐食することがなく、100%リサイクルが可能という特徴をもっている。
またZF社のプラスチック製エンジンマウントは、モジュラー化された構成により、様々なタイプのエンジンと車両に対してどのようにも組み合わせることができる設計になっている。
エンジンマウントに求められる特性をプラスチックで実現するため、ZF社は革新的な数値解析手法と製造プロセスを連携させてこの製品を生み出している。CAD(コンピューター援用設計)によるモデルを構築し、最新のシミュレーション・ツールを使って、様々な角度から解析を行い、最適な解答を導く作業が行われたという。その結果ZF社は試作と実験を繰り返すことなしに量産品に近い部品を生み出すことができるようになり、開発のサイクルは劇的に削減された。
微細構造の形や方向が一様なものではない、いわゆる「異方性」を再現したシミュレーションを駆使することで、重量を削り落とす部位やガラス繊維の配列が決定され、必要に応じた製品を作ることができるのだ。実際、こうした技術、開発プロセスを駆使し、ZF社はすでに繊維強化・複合プラスチック製のリーフスプリングを試作し、これを採用した軽量リヤサスペンションなどもプレゼンテーションしている。
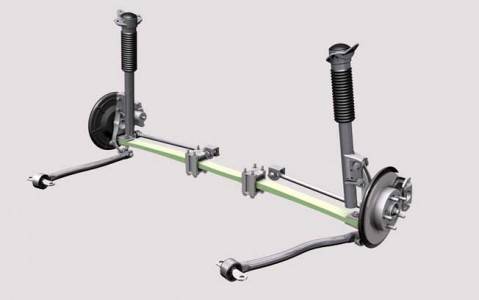