世界的システムサプライヤーのZFは、乗用車および小型商用車向けの最新世代となる電動ドライブを発表するとともにワークショップを2022年11月に開催した。
ワークショップはZFの電動化のキーとなるドイツ・シュバインフルトで行なわれ、冒頭、ステファン氏の基調講演で、まずZFの売上高は2021年、383億ユーロ(5.5兆円)、15万7500人の従業員、そして31カ国188箇所に生産拠点があるグローバル・システムサプライヤーであることが伝えられた。
そして次世代モビリティを開発することが戦略的な目標で、個人の移動から貨物輸送に至るまで、あらゆる輸送に対してソリューションの提供をしていくとした。
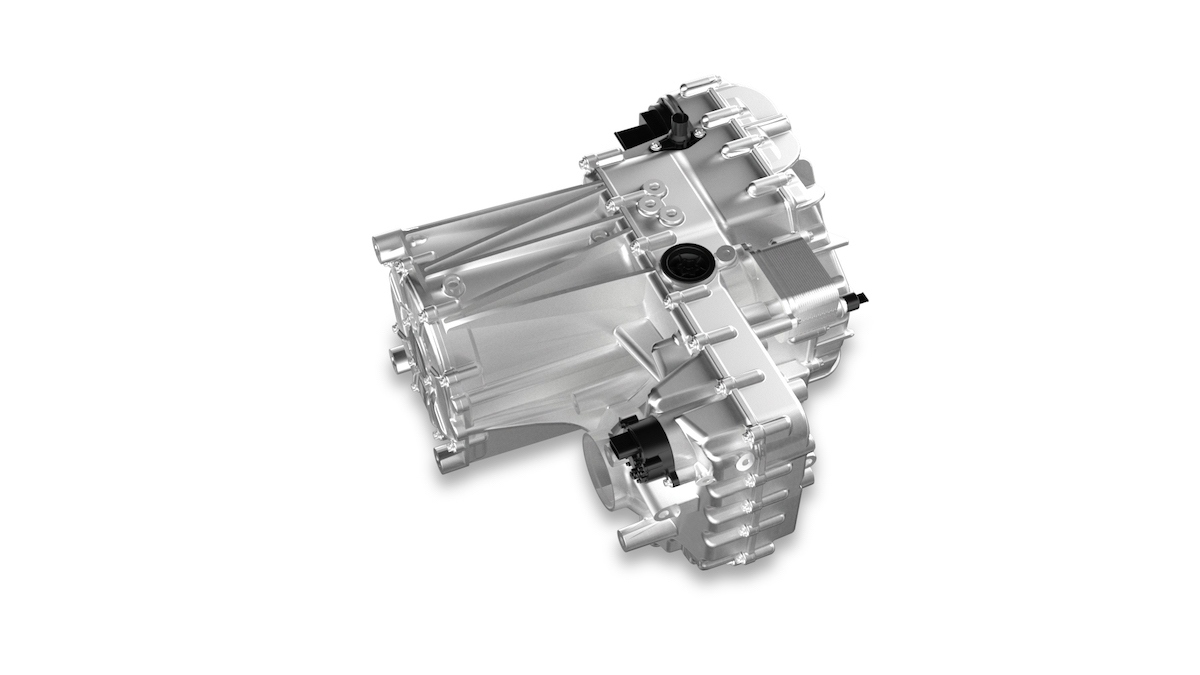
そのために、ZFは車両運動制御、統合安全性、自立走行、電動モビリティという4つの技術領域で未来のモビリティを形作っている。そして近年、世界の主要地域ではtank to wheelの規制が年々厳しさを増し、そのため、すべてのカーメーカーがポートフォリオの電動化を進めている現状がある。一部のメーカーではこの10年で100%EV車にしていく企業も出てきているわけだ。
そうした中、ZFでは電動モビリティとその製品群の最新開発に焦点を当て、パワーエレクトロニクス、e-モーター、メカニカルコンポーネントの分野における新たな開発に注力し、半導体ではシリコンから、SiC(シリコン・カーバイド)への移行、そしてGaN(ガン・ガリウムナイトライド)への移行は成功への重要な鍵の一つになると予測していると説明した。
特にインバータはe-ドライブの中核となり、半導体は2030年まで急速に需要が高まり、そして、ドライブトレインにおける更なる技術開発は、効率化がキーになるという。
400Vから800V、シリコンからSiCへ
具体的には従来の車両レベルの仕様に加え、設計電圧が最も影響力のあるポイントに挙げられている。このため、パワーモジュールのパッケージ材料には、より高いスイッチング周波数、電力密度の増加、動作温度の上昇が要求され、更なる課題が出てくるという。
現在主流の400V技術は2028年までに一部800Vに置き換えられ、その時点で800Vが400Vインバータの市場規模を超えると予想している。400Vのインバータはシリコンで開発され、800VではSiCで開発されることになり、2030年にはSiCのインバータが66%になると予測している。
またZFは、AWDセグメントの世界的な伸びを考慮し、1台あたり1.3個のe-ドライブを搭載することを想定している。つまり、2030年には、4700万台のEVが6100万ユニットのe-ドライブユニットを必要とするとしている。そして2025年にはSiCのインバータ搭載車に切り替わり、e-ドライブの効率は7%向上させることができるとしている。さらにその先はガリウムナイトライド(GaN)への移行が成功への重要なキーになると考えているわけだ。
ZFならではのストロングポイント
ZFの電動化技術の開発を遡ると、2005年からe-モーターの開発を始め、2008年に生産を開始。その数年後からe-アクスルの開発を始め、2018年に400Vのシリコン・パワー半導体ベースのアクスルを作っている。
次の大きなステップとなったのは2022年にローンチした800VのSiCの開発で、インバータに一部組み込んだアクスルにした製品だ。この構造でTier1が開発する800VのSiCを持っているアクスルは、ZFが世界で最初のサプライヤーであり、ZFだけが供給できているアプリケーションなのだ。
そして2025年に次の世代のアクスルに進化し、それはコンパクトでスケーラビリティを持ち400Vと800Vの仕様が存在する。そして完全に統合されたインバータを搭載していることが重要だという。というのは、統合されたe-アクスルによってドライブトレインのパッケージングが楽になり、1kWあたり30Nmが36Nmへ、そして51Nmまで進化させることが可能で、こうしたことを市場は求めているのだと考えているわけだ。
そして今回のワークショップのメインテーマとして「テクノロジーとイノベーション」を掲げ、ZFがどのような取り組みやソリューション、アプリケーションの提供が行えるかという具体的なUSP(Unique Selling Proposition)の解説が行なわれた。
それは高度なシステム専門知識とコンポーネントレベルでの強力な革新性、および重要なソフトウエアの機能を追加する能力を兼ね備えたものであり、さらに高いインターフェイス能力によりシステムをユーザー(OEM)のアプリケーションに最適な形で統合でき、システム全体を最適化することが可能であると説明している。
つまり、高い専門知識と経験を持つZFが開発したアプリケーション、ハード、ソフトの全方位ソリューションでカーメーカーのニーズに応えることが可能であり、カーメーカーのこだわりの部分に対しての擦り合わせもできる余地を残した取り組みであるというわけだ。
それでは、ZFのUSPとなる乗用車、トラック、商用車にむけた革新的な最新e-モジュールシステムのコンポーネントについて、e-モーター、減速機、DC-DCコンバータを見ていこう。
現在のEV市場における3つのポイント
電動パワートレインシステムの責任者であるマークス・ショワーべ氏のプレゼンテーションでは、e-ドライブ プラットフォームの考え方から説明があった。
プラットフォームを開発する場合、アプローチは2パターンあり、一つはインバーターやe-ドライブのコンポーネントからシステムを組み立てる方法で、これを「Lego Way」と呼び、逆にシステムが先にあって、そこからコンポーネントを導き出すやり方もあり、ZFではこの後者のアプローチで開発しているという。
そしてe-ドライブ プラットフォームを提供している現在のEV市場について、3つのポイントを挙げていた。それはまず、コストについて。以前はドライブトレインが主要なコストだったが、いまはバッテリーに代わっている。
次に、バッテリー容量により変化する航続距離だ。現在はEVの普及に十分な充電インフラではないため、逆に長い航続距離が必要になっていると考えており、これは特に欧州に当てはまるもの(日本ももちろん)だとしている。
航続距離はバッテリー容量を意味するが、容量を増やせばコストが上がり、重くなり、スペースも狭くなる。レアメタルの採掘も必要になりエコロジカル・フットプリントも悪くなる。だからバッテリー容量で稼がず、効率を上げることで航続距離を伸ばすことができるのがZFのソリューションであると。
次にドライブトレインの性能では、エモーショナルな要素が必要で、運転する楽しさは要求される。とくにアメリカのマーケットではドライビングダイナミクスが重要であるという。
つまり、コスト、効率、性能に対応するソリューションをZFは持っており、特にそれは「チャンピオンe-アクスル」というもので対応しているという。
チャンピオンeアクスルとは
・コストチャンピオンは、最高の低コストに焦点をあてているソリューションで、手頃な価格で提供できる。
・エフィシェンシーチャンピオンは効率を上げることで航続距離が稼げる。
・パフォーマンスチャンピオンはトルクとパワー密度を高めるもので、ドライビング・ダイナミクスを満足させるチャンピオン。
という、この3つのチャンピオンはさらにカスタマイズができる。つまりカーメーカーからの要求事項のリストに対し、システムドラフトに盛り込み、システムドラフト案ができたら上記の、どのチャンピオンがもっともニーズに対応できるのかを当てはめてみる。この時点で作業は80%終了できたことになるという。
あとはメーカーの要求に合わせてカスタマイズし、アジャストさせて納品ということになるが、そうした柔軟性があるモジュールを提供できることがZFのソリューション、アプリケーションの特徴でもあるという。
モジュール式プラットフォーム
続いてシャラー氏の講演ではさらにプラットフォームの次世代について詳しく述べていた。
まず、プラットフォームへのアプローチを考えた時、ひとつのパッケージにまとめるべきかを考えるが、前述のように市場からは複雑な要件を求めるので、ひとつのパッケージにしたプラットフォームではなく、モジュール式のプラットフォームが良いと判断しているという。
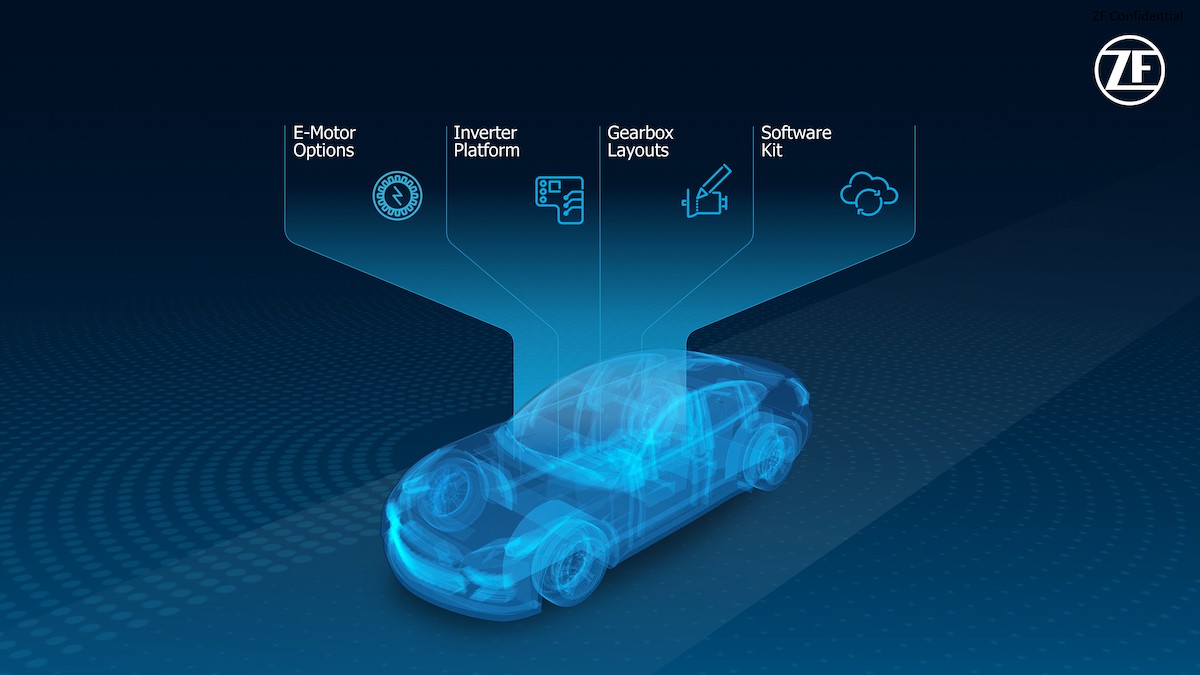
プラットフォームにはモーター、インバータ、ギヤボックス、ソフトウエアがあり、それらをモジュールに分ける必要がある。
中でもインバータ・プラットフォームについては、さらにモジュールからのアプローチを離れ、DDPのアプローチをとっている。つまりディスクリートなアプローチだと説明する。ディスクリートとは、ひとつの半導体素子で構成するチップのことで、それをダイスレベルで構成すること。ダイスレベルとは個々の半導体チップのことで、回路を焼き付け、格子状に切り分け得られたチップを意味している。
ダイスはモジュール化とは違ったアプローチで、80〜350kWまでのスケーラビリティがあり、その際にインバータを変える必要がない特徴がある。またインバータのソフトウエアの変更も不要だという。つまりそれは、開発時間を短くするのに大きな魅力的性能であり、ダイスレベルでスケーラビリティを確保しているというわけだ。この特徴はトポロジー(位相幾何学)をキープしていることで、変換しても維持される図形的性質を利用しているため可能にしているという説明だ。
ノウハウを活かしe-アクスルでも実現
ソフトウエア開発では、ハードウエアを交換することなく、進化できることをすでに我々は経験している。同じことがe-ドライブでできるのだという。
ソフトウエアキットのいいところは、モジュール化されていることがひとつの特徴で、ユーザーによっては自身の持つモジュールをZFのソフトウエア・モジュールとインテグレートする必要があると考えるOEMがいる。しかし、ZFのソフトウエアキットは、これに全く時間をかけずに統合することが可能で、さらに、いろいろなインバータに対応できなければならないが、それを前述のDDP(ディスクリート・ダイス・プラットフォーム)を使って実現しているという。
3つ目はZFのレガシーである。ZFは過去にハイブリッドに関しさまざまなアプリケーションを開発してきた。このアプリケーションがドライバビリティを実現し、運転した時のドライブフィールを形作るノウハウを持っている証拠でもある。またそれぞれのブランドのDNAに合致させることは過去数年間にわって実施してきた。これがレガシーであると。
同じことをe-アクスルでやっているのだと説明する。ハイブリッドのパワートレインと同じことで、ギヤがないという違いだけだと。それはカスタマーに対するUSPであるとも。
具体的にはZFのe-アクスルは、非常にフラットで縦置き、横置き、どの方向でも使える特徴がある。横置きであればリヤのアクスルに使い、縦置きにすればフロントアクスルに使うなど、非常にコンパクトで剛性が高くNVH(Noise Vibration Harshness)に貢献できるe-アクスルということだ。
新たな冷却と巻線の技術を採用したモーター
ローランド・ヒントリンガー氏のプレゼンテーションは、モーターに特化した2つの最新技術に関するプレゼンテーションだった。
ひとつは冷却に関するもので、もうひとつは巻き線技術だ。まず冷却に関し、ステータの外部にウォータージャケットがあり、水を循環させている。そしてステータのチャンネルクーリングを行なう。これはより熱源に近いところですぐにクーリングできるアプローチができ、冷却媒体にオイルを使って冷却する技術。これは、すでに量産している技術でもある。
次に巻き線技術については、現在の主流はヘアピン銅線技術であるが、次のステップは、イノベーションの余地があると考えている。そこで考え出されたものは、ブレーデットワインディング技術で、ブレーデットワインディングとは、編み込み加工方法のことで、編み込まれた銅線をステータ内に入れる。ヘアピンの場合は溶接ポイントが200、300箇所必要だったが、このブレーデットワインディングでの溶接は、接続ポイントだけになるので20箇所の溶接点だけで済む。
これは非常に大きなメリットであり、ワインディングの大きさも50%削減できる。つまりコンパクト化できるわけだ。またこうしたスロットクーリングで重希土類の削減にも貢献できるという。つまり熱の影響をうけないために重希土類を使用しているが、クーリングすることにより、重希土類を1%までに削減できると説明している。
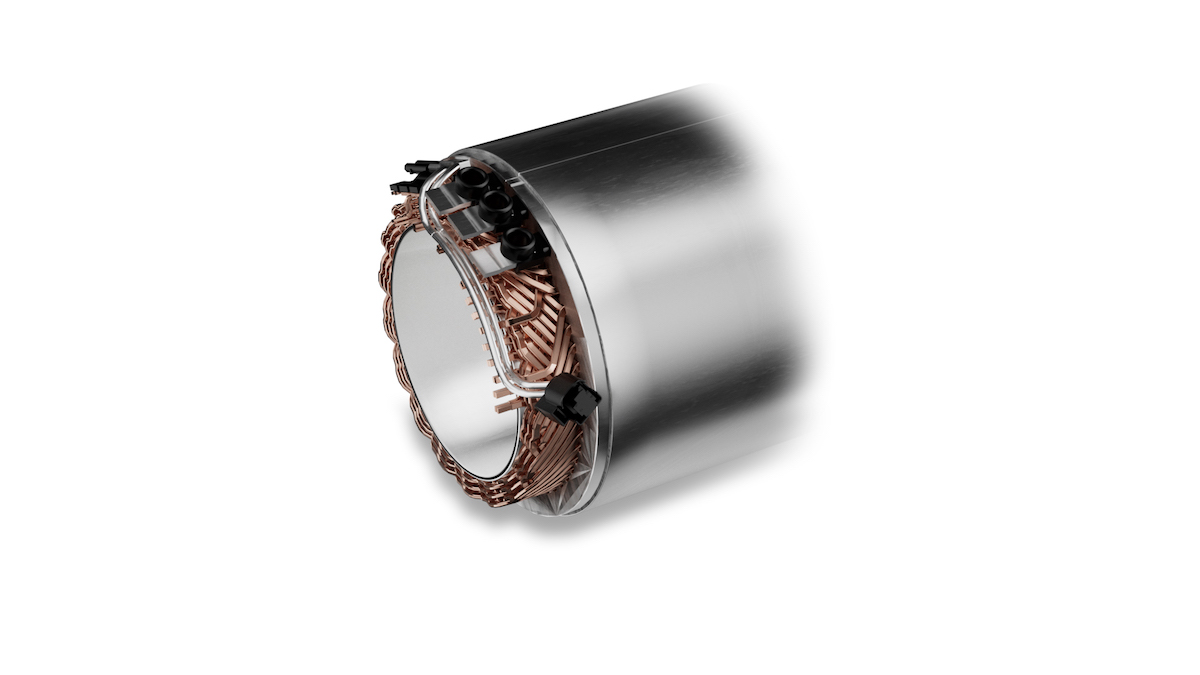
減速機とDC-DCコンバータ
ロバート・ピーター氏は減速機についてプレゼンテーションを行なった。減速機はモーターの高速回転を減速させるが、トランスミッション効果でトルクを上げることができる。だが、2スピードで足りてしまい、2速以上が必要になるのはスポーツカーや特殊な用途の車両になる。また減速機は最大速度の課題を解決するアプリケーションになるという。
そのZFが開発した最新の減速機のジオメトリーとアーキテクチャーについての解説があった。ひとつはオフセットデザインと呼ばれるもので、この場合はモーターとアウトプットの軸とがセパレートされた構造になっており、新たに開発した減速機ではモーターと出力軸が共通になっている。
市場のニーズはノイズであり、これが重要な要素で、NVHの良いパフォーマンスが求められつつ、効率性の高さも求められている。新しい減速機は、トランスミッションによるロスを減らすことで効率をあげ、重量を減らし、そしてトルクを上げることでパワー密度を上げることができるものだ。
そうした構造を実現するために、パッケージングの工夫が必要で、オフセットデザインでは2つのヘリカルギアを使い、ベベルギアを使ったデファレンシャルでトルク配分をしている。これは2011年にローンチした2in1システムとして市場に提供している。
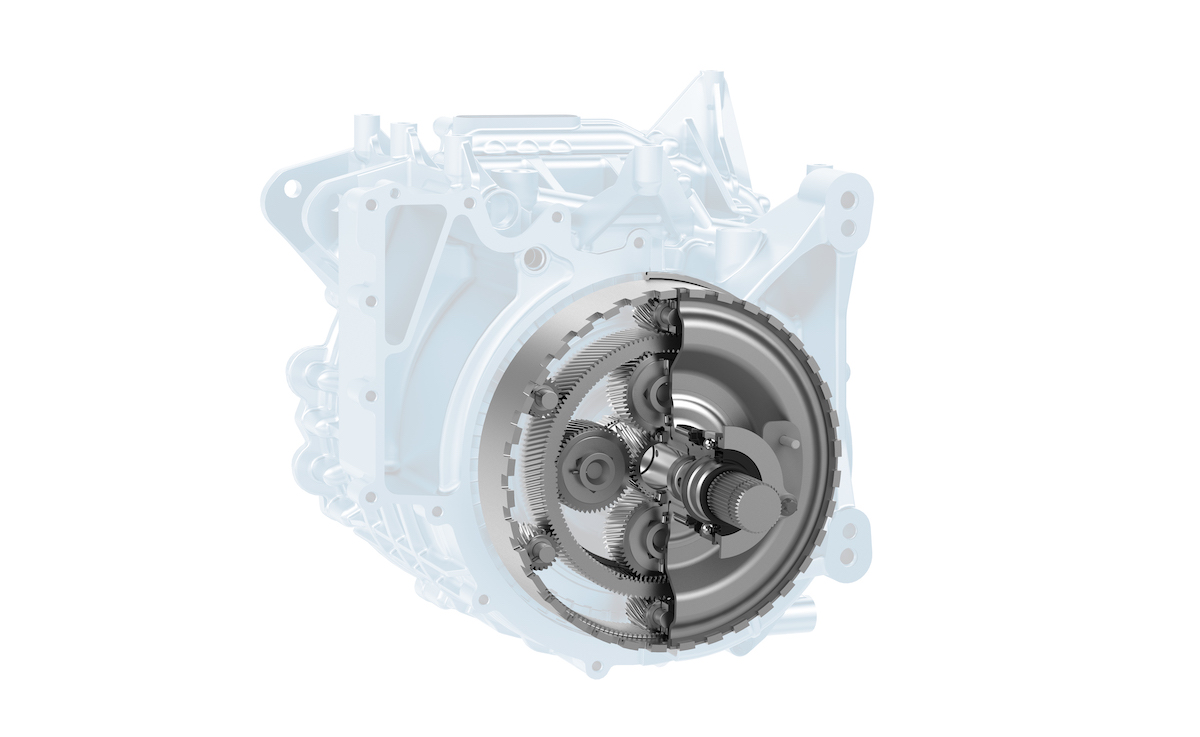
新開発のeVD3(electric vehicle drive)は3in1システムになっており、出力軸共通で2つのプラネタリーギヤのセットを使っている。
これはトランスミッションとデファレンシャルの機能を統合した機能を持っており、モーターのシャフトは内側のプラネタリーギヤのサンギアに接続され、キャリア側はホイールにつながる。外側のリングは反対のホイールにつながっている構造だ。こうすることで、50%ずつのトルクスプリットが可能になっている。
eVD3の設計製造は9HP(エンジン横置き用9速AT)のノウハウが生かされており、コンパクトで軽量にできている。ディスクの幅は50mm〜60mm程度の幅しかなく設置スペースが小さいので、従来のオフセットデザインの2in1よりコンパクトなスペースに搭載できるのが特徴だ。
結果的には25%程度のサイズダウンができるとし、パワー密度も上げられ10%の軽量化ができる。さらにトランスミッション・ロスは20%削減でき、オフセット型2in1より20%ロスが少ない減速機というわけだ。
最後はカーステンゲッテ氏がシュバインフルト技術センターから講演したのが、DC-DCコンバータだ。ZFでは現在燃料電池システムを商用車向けに開発しており、FCV用の高電圧DC-DCコンバータがこれまでなかったという。
燃料電池側の電圧は15V-400Vという環境であり、e-ドライブシステムは400Vで稼働している。さらに今後は800Vになるので、いままではこれをつなぐものが存在せず、ミッシングリンク・エリアとして新規開発したという。それが一方向の高電圧DC-DCコンバータというわけだ。
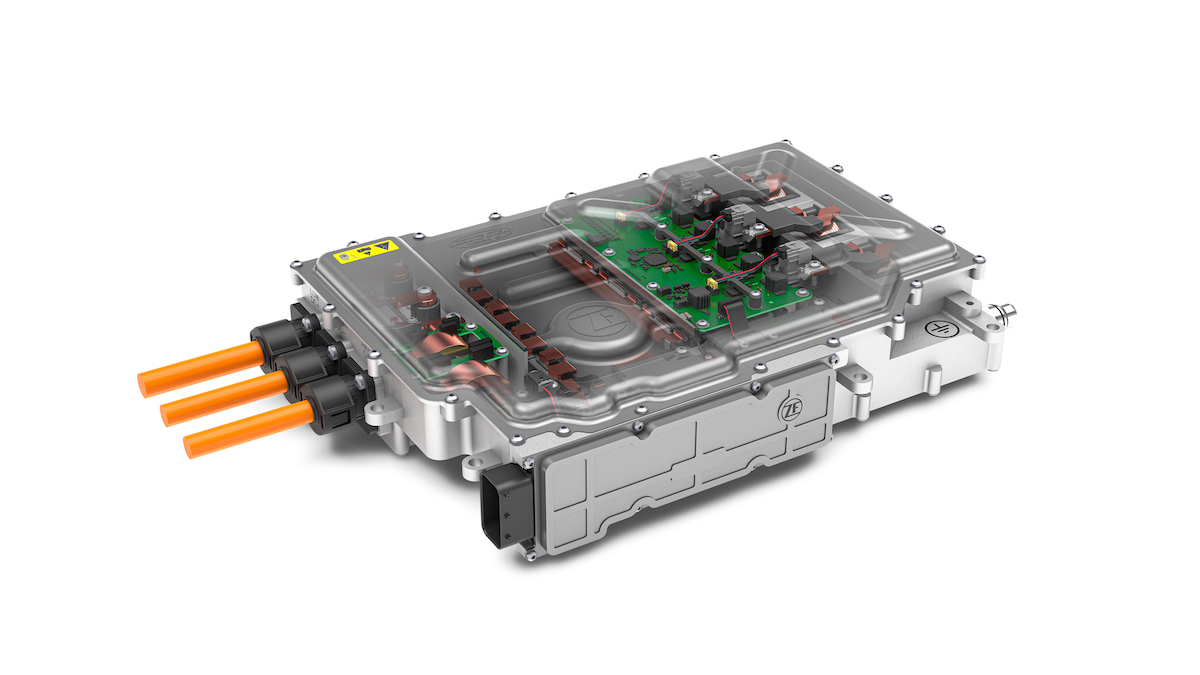
FCV用の高電圧DC-DCコンバータ
ZFの最新世代e-ドライブまとめ
まとめてみると、ZFではより小さく、より軽く、よりパワフルなe-ドライブを乗用車と商用車向けに開発した。
• e-モーター、パワーエレクトロニクス、トランスミッション、ソフトウェアからなるシステム全体で、優れた出力密度と効率性を実現している。
• 3 つの基本構成からなる最適化されたモジュラーコンセプトによる最大限の柔軟性がある。
• コンパクトな設計で省資源化を実現。
といったUSPを持ちつつ、これまでのICE時代に培ったノウハウと知見を活かし、アプリケーション単体での販売も行なう。またソリューションとしての提供はもちろん可能で、かつOEMのオリジナル制御とのインテグレートも容易に可能なe-ドライブトレインに位置付けているというわけだ。