トヨタは2023年6月13日、次世代の新技術発表を行なった。そこでは、これまで強調してきた水素利用のクルマ以外に、電動化、EV化にも全力を注ぐことがアピールされた。
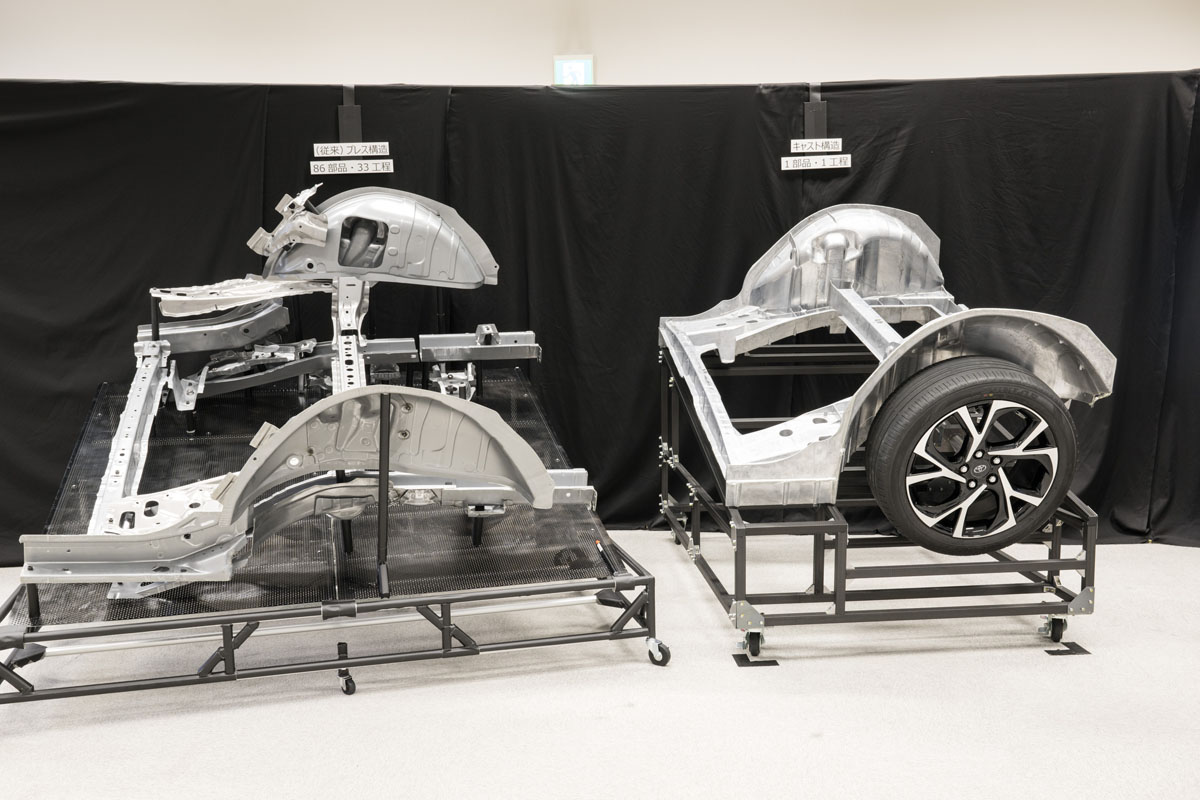
発表された技術は多岐にわたるが、まずはEVの製造技術に関しての訴求が採り上げられている。
トヨタはこれまでにEV車としてレクサス・ブランドでUX300e、RZ450e、トヨタ・ブランドでbZ4Xを発売しているが、その生産はサブ・ラインでの少量生産で、bZ4Xは元町工場のMIRAIとの混流生産、つまり極小規模生産であり、収益性は厳しい状態にあった。
本格的なEVを生産するためには専用のラインが必要であり、収益性を高めるには、より大量で、より少ない工程で生産する必要があるのだ。
その背景には、リチウムイオン・バッテリーの価格は、韓国、中国のメーカーが世界規模で大量生産しているにもかかわらず、依然として売り手市場であり、バッテリー価格の大幅な低減は期待できなくなっている。
そのため、EVの生産コストを引き下げ、収益幅を拡大するには、大量生産と生産方法の革新が必要で、より合理的に、より短時間で組み立て生産をする必要がある。
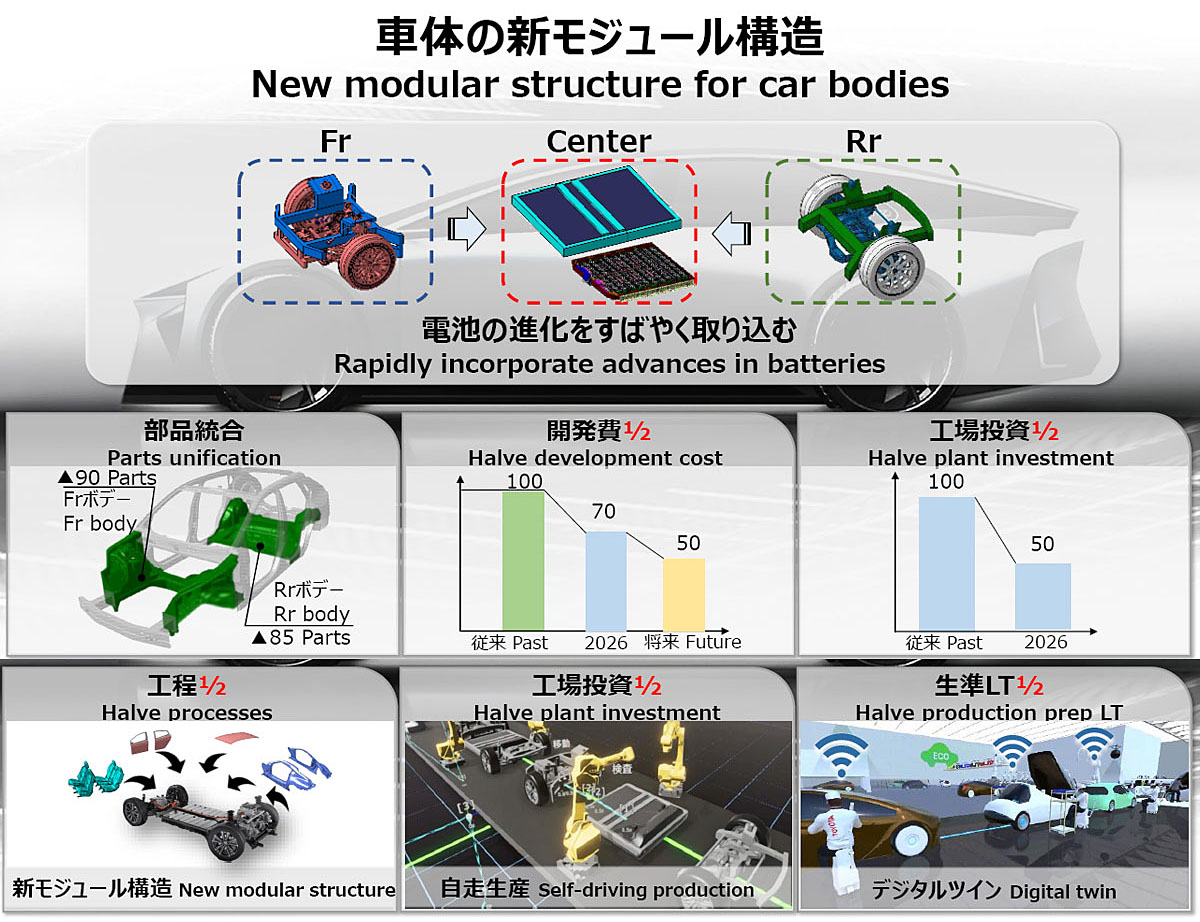
トヨタもギガプレスで生産
そのパイオニアがテスラで、組み立ての大幅な自動化はもちろん、モデル3以降はリヤセクション、フロントセクションをアルミで一体成形する、ギガプレスを採用している。
これは従来の自動車メーカーにはなかった着想であった。一体成形により、従来のようなサブフレームや、それに取り付ける部品が省略され、プラットフォームへの組み付けも一挙に行なうことができ、組み付け時間を大幅に短縮できる。まさにモジュラー組み付けとも呼ばれる方式である。
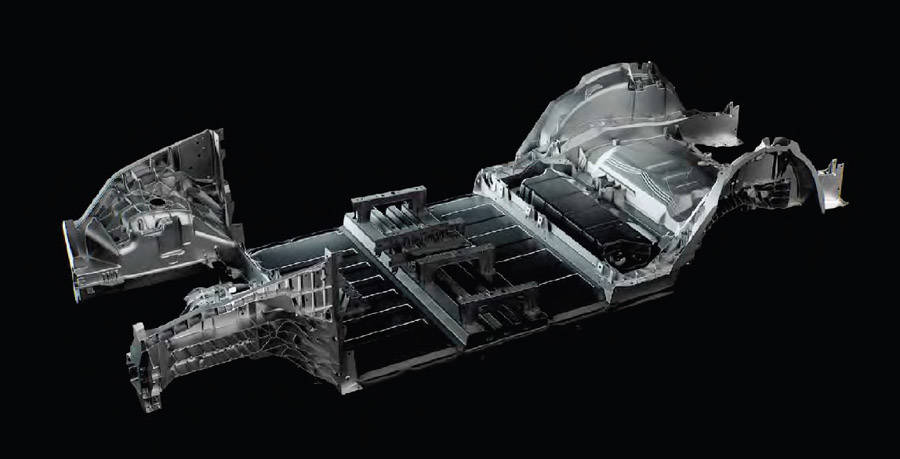
この発想は、テスラに始まり、既に中国のEVメーカーは採用しており、トヨタが追いかける形になる。ちなみにテスラの上海工場は年産200万台近い生産規模といわれており、EV生産の規模は他社を圧倒している。
トヨタはEVとしての特性をより生かした次世代EVの開発・生産において、部品の統合=モジュール化、生産準備工程の半減、生産工程の短縮、ひいてはEV製造工場に対する投資額を従来の規準から半減させることを目指している。つまり生産の原単位を最小限まで抑えることで、収益を確保しようとしているのだ。
部品の大幅なモジュール化は、まさにテスラ方式のギガプレスの採用であり、トヨタは今回この方式を採用することを強調している。
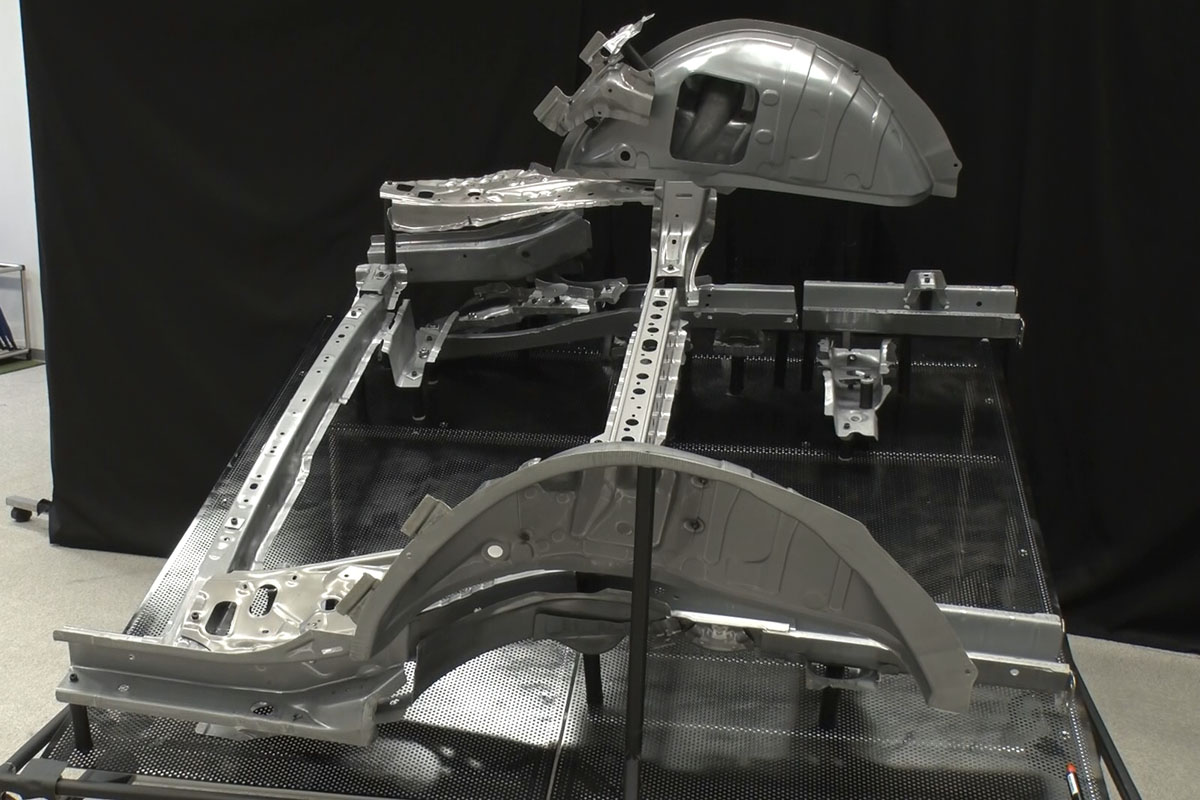
ただ、前後のサブフレームや構造材をアルミ材で一体鋳造プレスを行なうためには、6000トン〜1万トン・クラスの鋳造プレス機が必要になるが、それをトヨタが導入するのか、サプライヤーが導入するのか?興味深い。
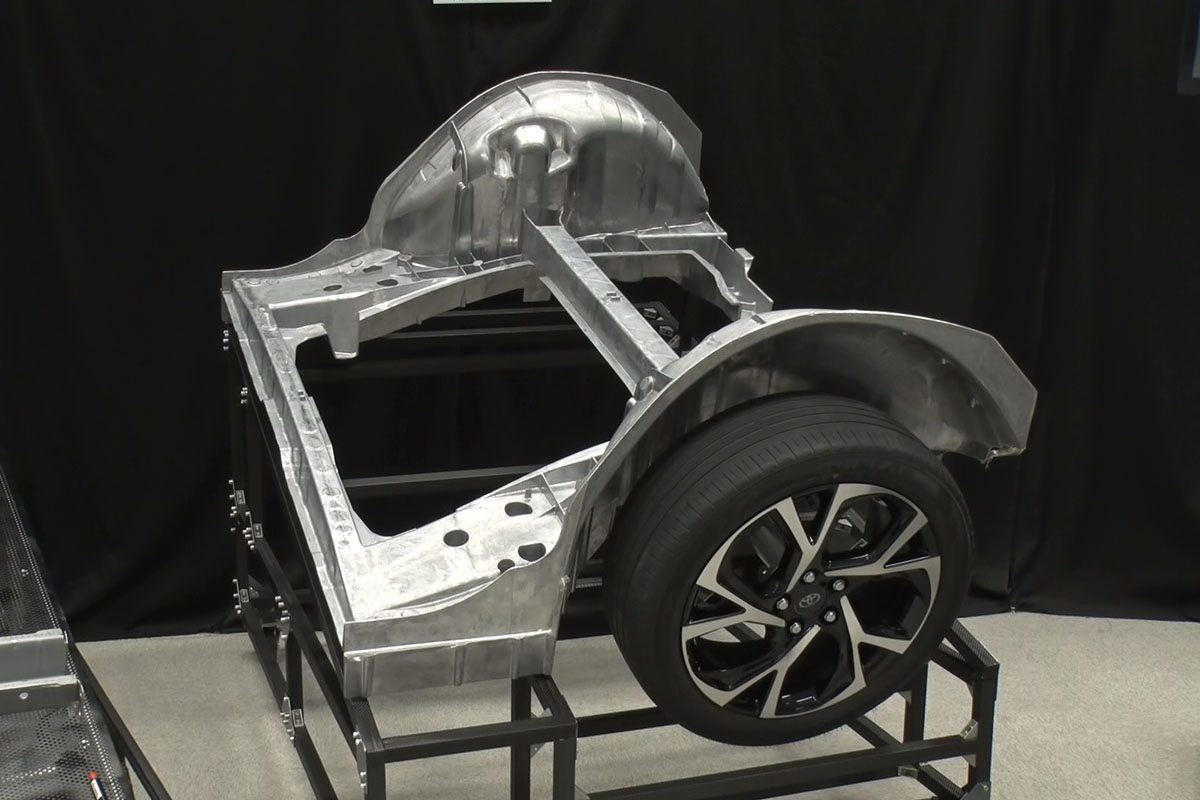
ギガプレス以外に、より革新的なEVプラットフォームの採用も必須となる。特にバッテリーパックを中国のBYDのように構造材とするのか、テスラのようなホットスタンプ材で支持するのか? プラットフォームとしてのフレキシビリティとEVならではの革新的な構造を両立することが求められている。
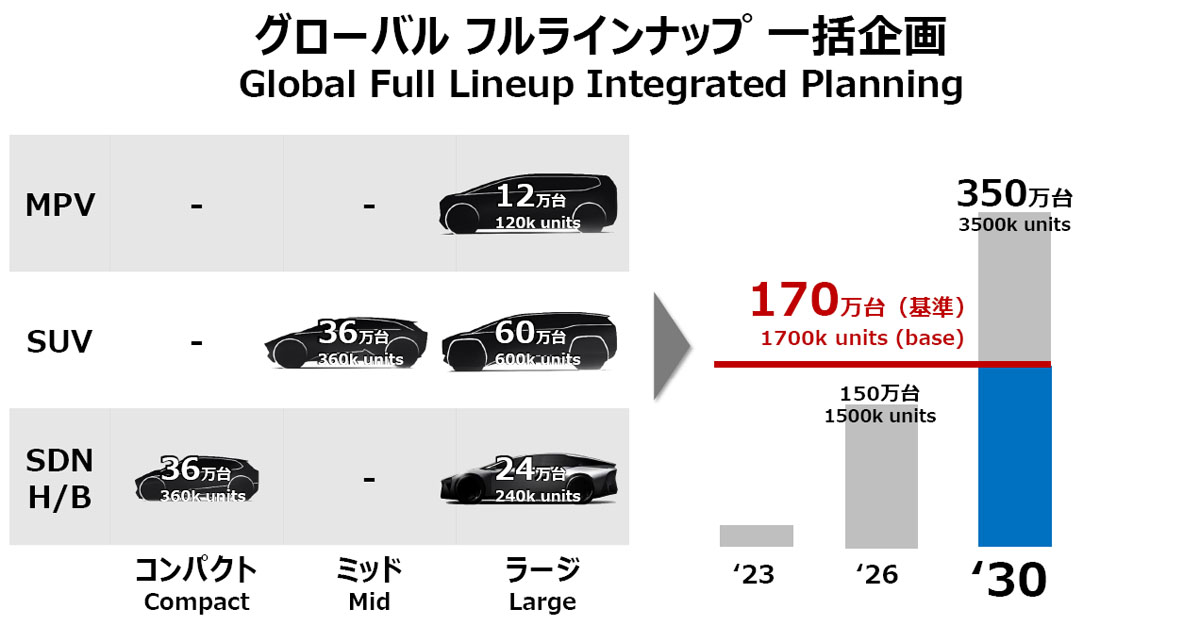
トヨタは2030年に電動車を350万台、その中でEVは170万台を目論んでいる。これを実現し、EVでの収益を確保するには、各種カテゴリーの車両一括企画、車両コンポーネンツのモジュール化、そして生産にける原単位の半減を行なうことが挑戦すべきテーマである。
このコンセプトにしたがって開発・生産される新世代のEVは2026年に登場する予定だ。