日産自動車は2022年4月8日、2028年度の量産、実用化を目標にして研究開発を行なっている全固体電池の積層ラミネートセルを試作生産する設備を初公開した。また同時に全固体電池の開発の現況をメディア向けに紹介した。
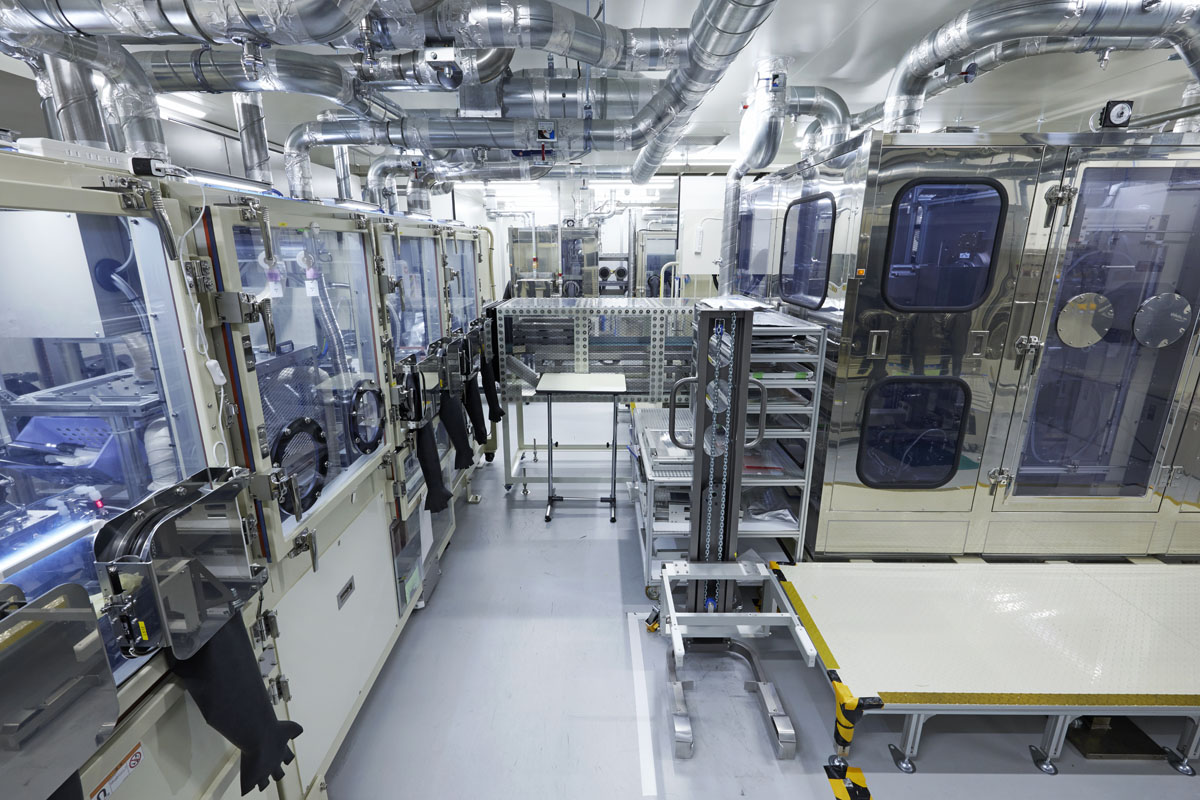
なお、今回の全固体電池試作のための設備は総合研究所(神奈川県横須賀市夏島)内に設置されているもので、つまり研究室段階での研究、開発、試作だ。
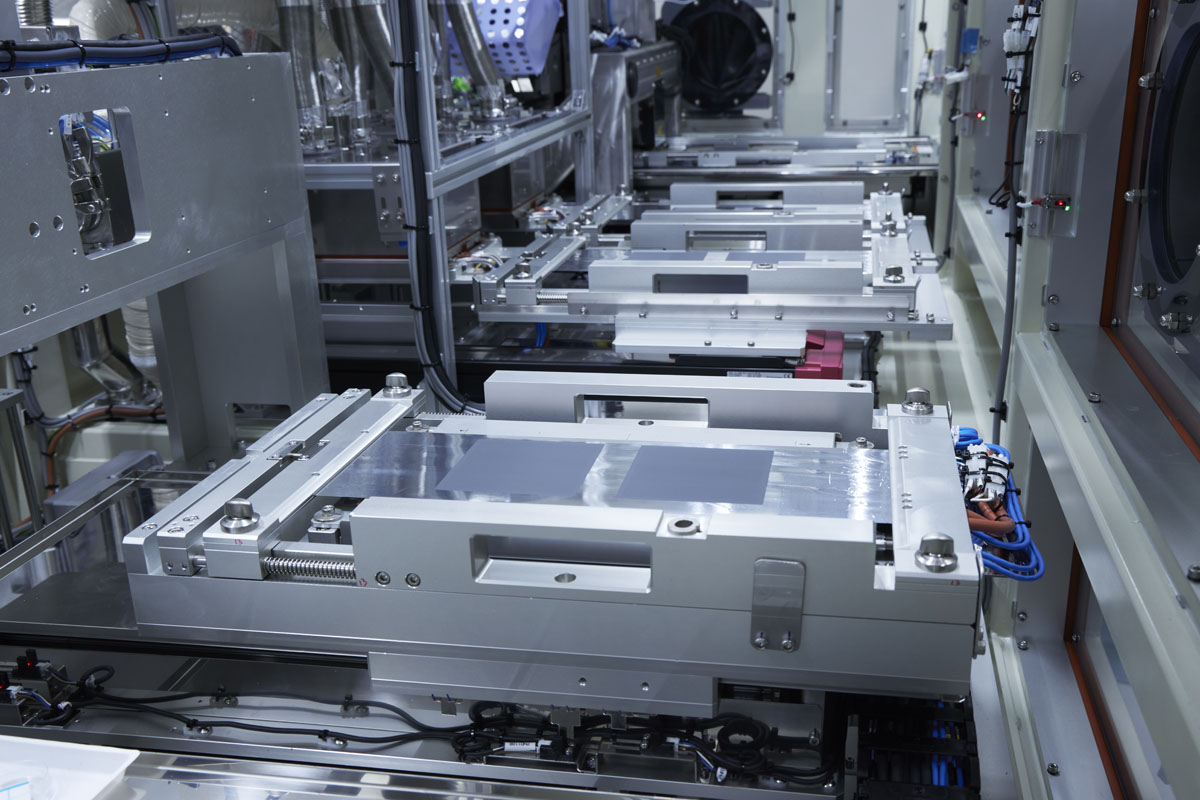
日産が発表している開発計画では、ルノー、日産、三菱のアライアンス内における次世代電池のリーダーを務め、現時点の総合研究所内での研究・試作から2024年頃には横浜工場内に全固体電池のパイロット・プラントを立ち上げて量産のための研究・開発を行ない、その成果をベースにして2028年度中に本格的な量産体制を整えるとしている。
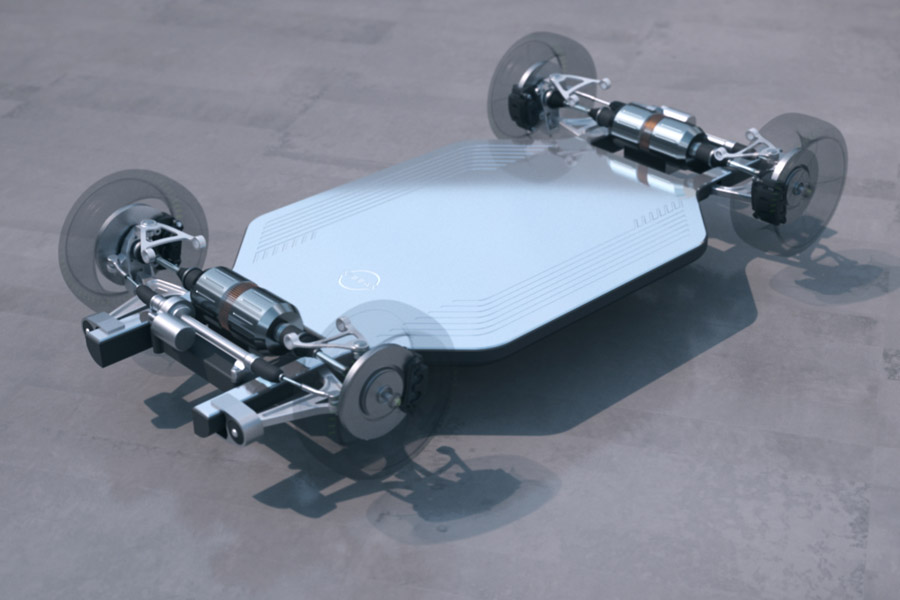
全固体電池が秘める様々な可能性
全固体電池は、現在の主流であるリチウムイオン電池を超える次世代の高性能電池として知られている。従来比で約2倍となる高いエネルギー密度、優れた充放電性能による大幅な充電時間の短縮、電池の温度耐性の大幅な向上、さらには現在のリチウムイオン電池より安価な材料の組み合わせによるバッテリーコストの低減などにより、電気自動車の性能、利便性などを飛躍的に向上させる可能性を秘めており、それだからこそ現在の世界中の自動車メーカー、バッテリーメーカーから大学の研究室までが全固体電池の研究開発に取り組んでいる。
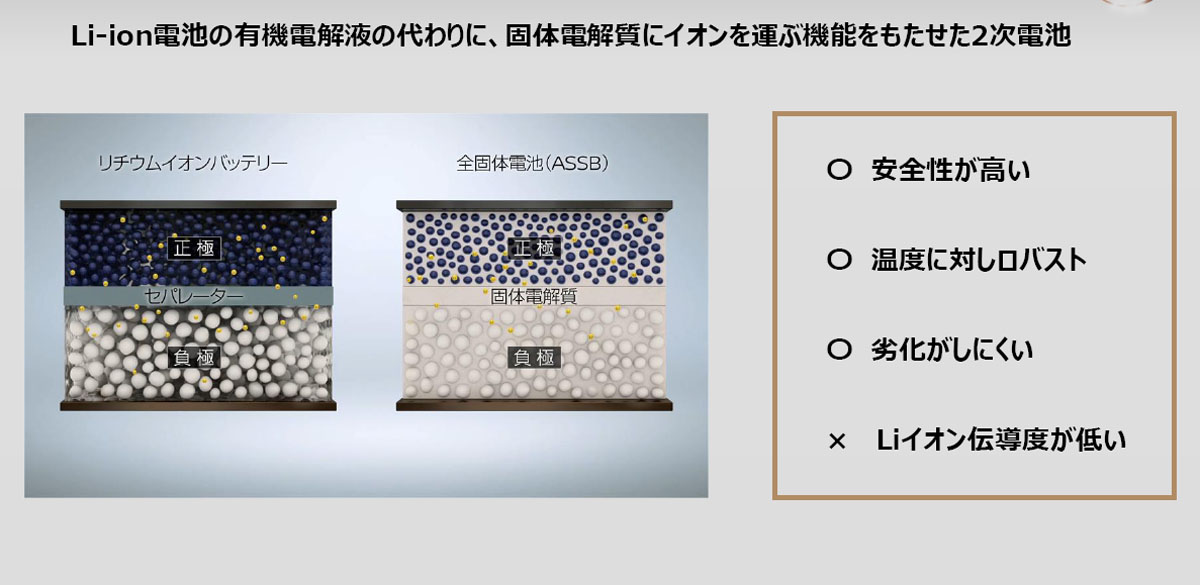
全固体電池は、リチウムイオン電池に比べて航続距離が2倍、充電時間が1/3、そしてリチウムイオン電池のような冷却・保温など温度管理が不要というポテンシャルを備えている。
また、全固体電池が低コストという理由は、現在のリチウムイオン電池がニッケル、コバルトなど高コストな素材を使用するのに対し、全固体電池は硫黄硫化物、マンガンなど低コストの材料が使用できるからで、全固体電池の価格目標は7500円/kWh以下とされている。現在のリチウムイオン電池が1万円以上/kWhで、改良型リチウムイオン電池の価格目標は7500円/kWhとされており、この価格が実現できれば従来の内燃エンジン車と同等の生産コストに納まり、収益性を高めることができるとされている。したがって、全固体電池で7500円/kWh以下の価格が実現すればまさにBEVの常識を完全に打破することができるのだ。
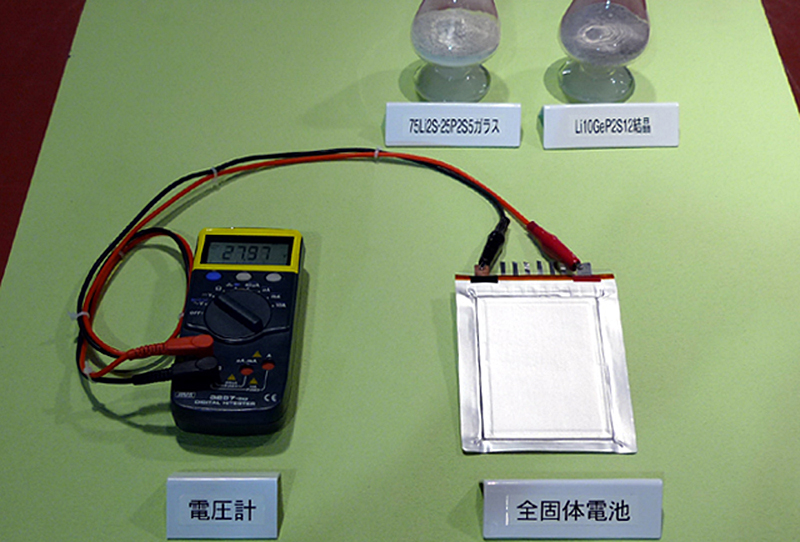
日本においても、トヨタは2012年の段階でリチウムイオン電池を超える次世代電池として全固体電池、リチウム空気電池の研究に着手していることを発表し、全固体電池の試作品も公開している。そして2020年にはコンセプトカー「LQ」で、公道走行試験も実施。しかし、BEV用としてはまだ課題もあることから2021年9月には2025年までにハイブリッド車用として搭載する計画であることを発表した。
またホンダも早い時期から全固体電池の研究、開発をなっており、2022年度中にはパイロット・プラントを立ち上げるとしている。
フォルクスワーゲン・グループも全固体電池の研究・開発に取り組んでおり、傘下の電池メーカー「ノースボルト」社と連携し、実用化を目指している。フォルクスワーゲン・グループの場合は開発だけでなく、生産プラントもノースボルト社で並行して立ち上げることが前提になっているのが強味となっている。
日産は、初代リーフ用にラミネート型リチウムイオン電池を開発し、世界に先駆けて採用した経験を持ち、ラミネート型リチウムイオン電池の開発以降も次世代の電池の研究を多角的に行なっており、当然ながらリチウムイオン電池のさらなる性能向上、全固体電池の素材の研究、生産方法の研究などを推進してきている。
2011年には固体電解質として硫化物系電解質を東工大・菅野了次教授が発見。従来の全固体電池用の電解質として酸化物系電解質、ポリマー系電解質が検討されていたがイオン伝導率が低いという欠点があったが、硫化物系電解質(リチウム・ゲルマニウム・リン・硫黄化合物:LGPS)はリチウムイオン電池の液体電解質に勝るとも劣らない物性であることがわかったのだ。
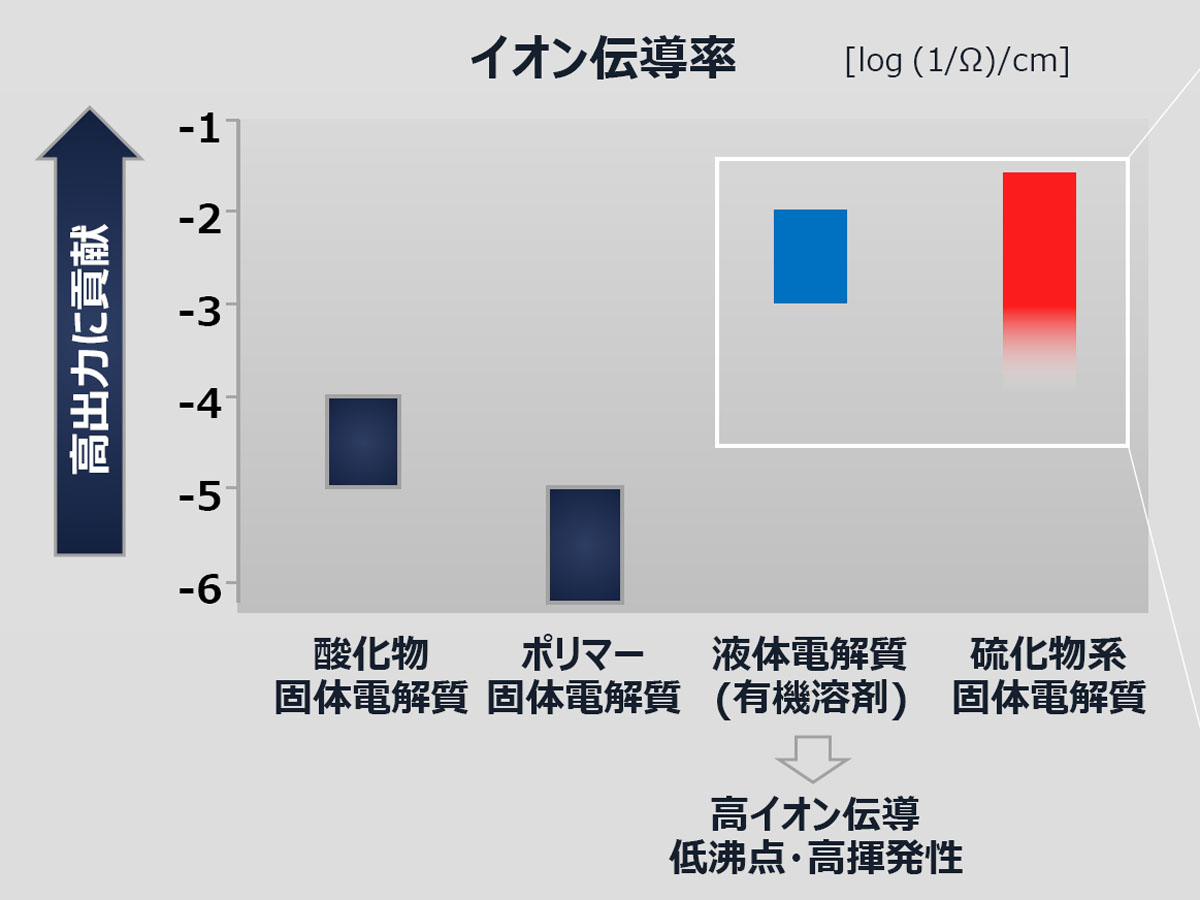
そして、現在はこの硫化物の電解質と組み合わせ、より高出力が得られ、かつ低コストの正極、負極の各材料の選択が行なわれている。正極はより低コストの硫黄マンガン材、負極はエネルギー密度を高めるリチウム金属系が想定されている。
ただ、量産するためには正負極材料と固体電解質間の高密度化、均一な界面形成と維持などを実現するために、使用する材料、電池の構造、生産方法など幅広い範囲での研究、開発が求められている。
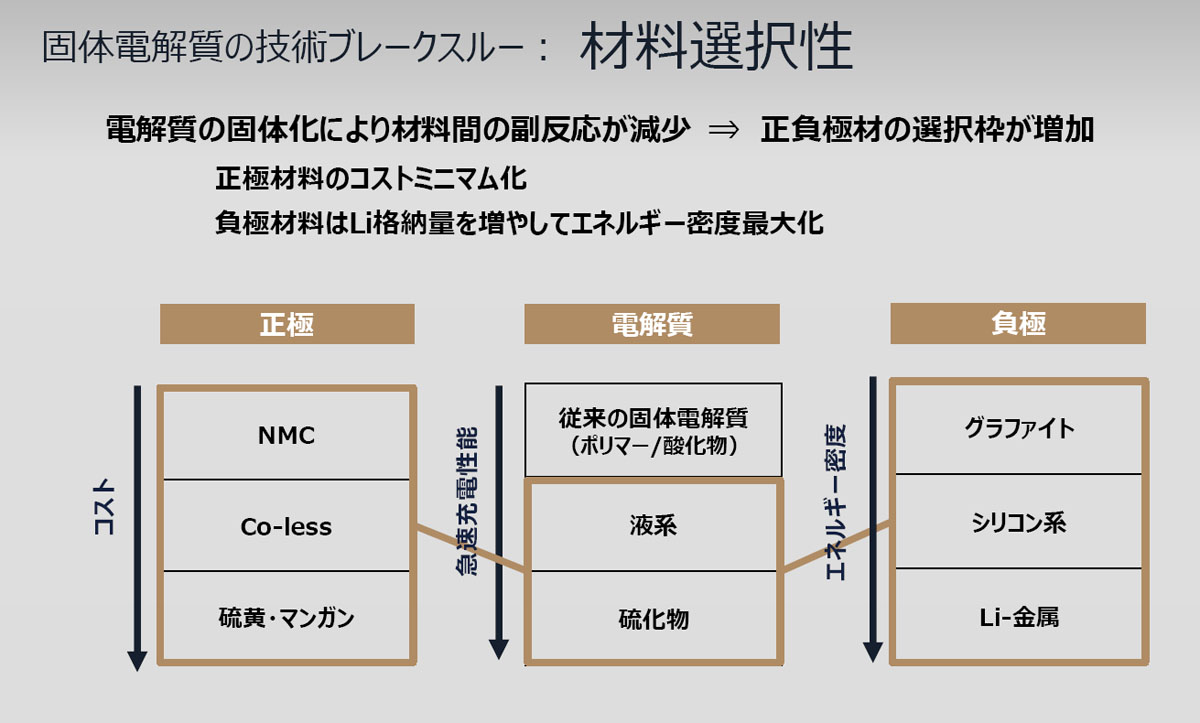
そのため、日産は世界の大学の研究室やNASAと連携し、材料の探索、材料機能原理シミュレーション技術、高イオン伝導・高耐久電解質材料設計法、高次元の解析技術の研究などを推進している。
量産化への課題
実は、この段階が量産化に向けて最も重要なポイントだ。現在のリチウムイオン電池の量産化の前には、ノーベル化学賞を受賞したスタンリー・ウィッティンガム博士は1976年に正極に二硫化チタン、負極に金属リチウムを使う二次電池に、リチウムのイオンを電荷として使用することを提案しているが、これが基本原理となった。そしてジョン・グッドイナフ博士らが1980年にコバルト酸リチウムが正極の材料に最適であることを発見。これらを前提に、1985年に旭化成の吉野博士が負極に炭素材を、正極にコバルト酸リチウムを使用することで4.0Vの高電圧を持つ現在のリチウムイオン電池の基本概念を確立。さらに吉野博士は電池の各種の材料や生産方法も開発することで実用化が実現している。つまりリチウムイオン電池も10年という時間を要して量産化された歴史がある。
全固体電池も、基本構造は確立されたものの、生産のためには最適な材料選びからそれらの生産方法などが確立されなければ量産は実現しないのだ。
もうひとつ大きな課題は、全固体電池特有の界面の安定維持である。バッテリー内の正極活物質は充電すると膨張し、放電すると収縮する。液体電解質ならこうした問題は発生しないが、固体では膨張、収縮により電解質の密着性が失われ、リチウムイオンの伝導は行なわれなくなる。全固体電池はラミネート構造だが、実際にセルの厚みは膨張、収縮により約5%ほども変化するという。
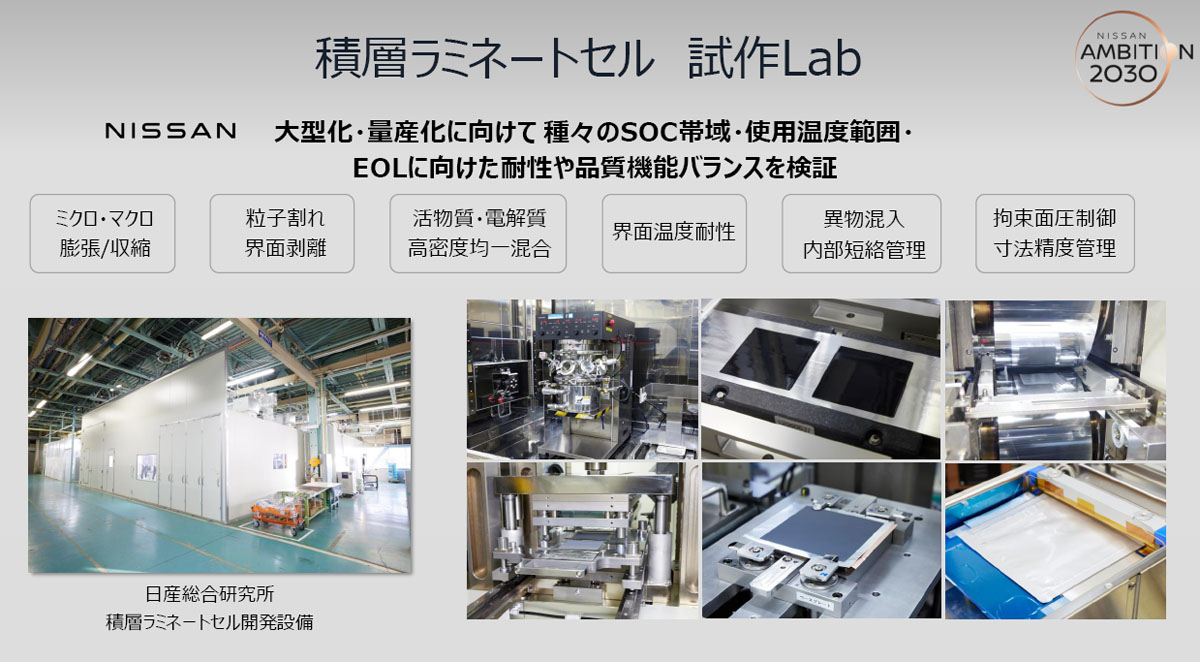
そのため、電極界面の変化を制御するためセルはリチウムイオン電池の3倍の高圧でプレスされ、ガラスのような硬さになる。と同時に膨張収縮できる構造でなければならないのだ。このあたりも生産のための重要なノウハウとなる。
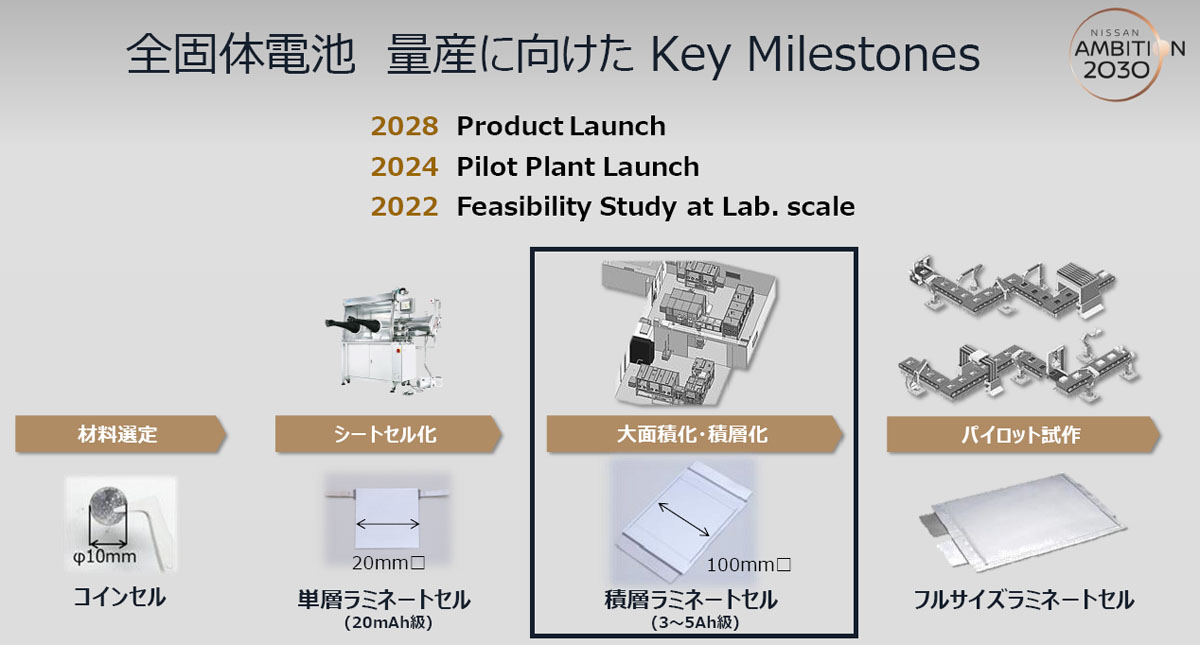
これらの課題に取り組むため日産は総合研究所のラボで試作を繰り返しているが、量産の前段階となるパイロットプラントの立ち上げに向け、今後さらに研究・開発を加速させていくことになる。<レポート:松本晴比古/Haruhiko Matsumoto>