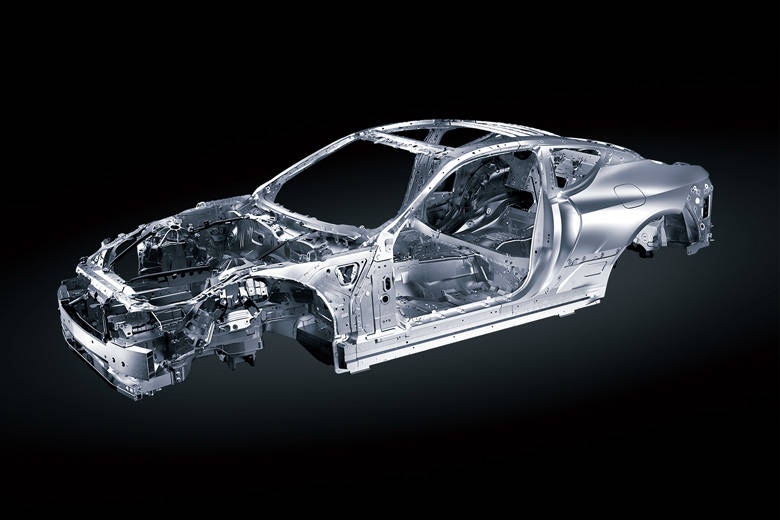
クルマに興味を持つ人にとって、エンジンやサスペンションはかなり気になるはずだ。馬力やトルク、サスペンションの形式などは、クルマ・マニアなら話題にすることが多い。しかし、さすがにボディとなると、カタログを見ても特に記載はないし、カタログ数字で比較できる物差しもない、じつに地味な存在だ。
■ボディの形式と基本構造
ボディそのものに踏み込む前に、まずはボディの形式を考えてみよう。クルマのボディの基本形はセダンで、セダンから発展したカブリオレ、クーペ、ステーションワゴンなどがあり、いずれも馬車の時代から存在している。
それ以外に近年では、2ボックス・ハッチバック、ワンボックス、ミニバン、SUVなどもボディ形式として加わっている。
しかし、ボディ形式は各種あっても、馬車の時代からボディの基本構造は、ベースとなるフレームの上にキャビン(コーチ)を架装するという方法で、馬車から自動車の時代を迎えても変わることはなかった。
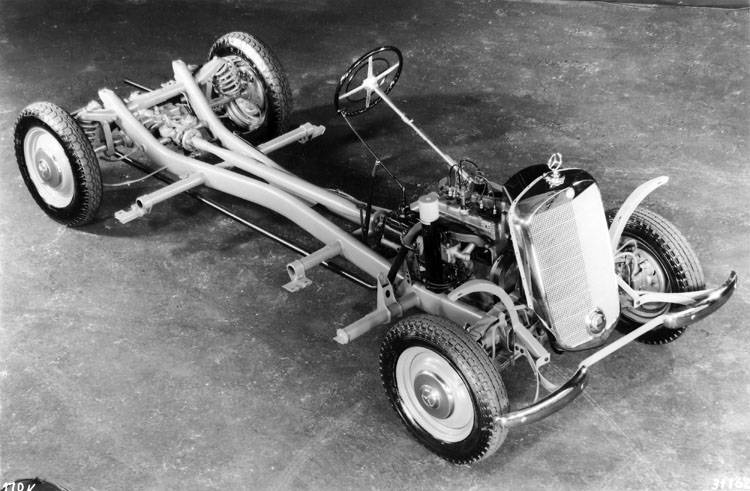
つまり自動車は、はしご型(ラダー型)フレームや、X字型のフレームといった基本フレームにキャビン(アッパーボディ)を乗せる方法で造られていた。この場合、路面からの入力を支えるのはフレームで、そのためには頑丈な木製、または金属でフレームが作られ、その一方で大きな強度を負担しないキャビンは、木製、あるいは木製骨格に薄い鉄板を張るといった構造になっている。
しかし、より革新的な自動車が第2次世界大戦前に登場している。シュタイヤー社のエンジニア、ハンス・ルドヴィンカはチェコのタトラ社に招聘され、1927年コンパクトカー「T11」を設計した。このT11はバックボーン・フレームを採用し、四輪独立サスペンションを持ち、フロントのエンジンからリヤデフへ繋がるプロペラシャフトはトルクチューブに内蔵した。そのチューブがフロアフレームを支える骨、つまりバックボーンを形成していた。
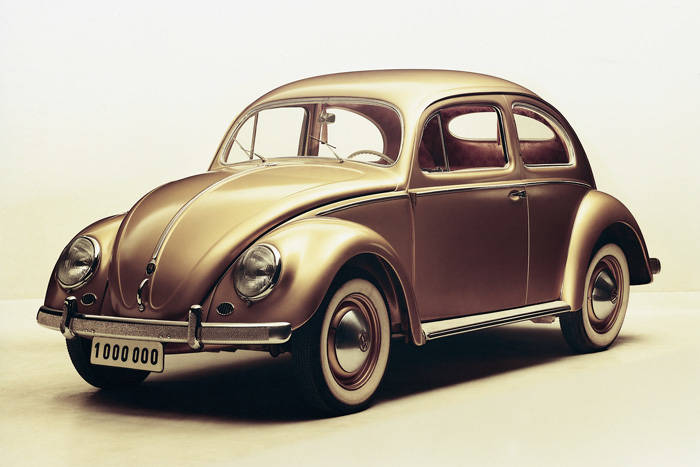
この着想を受け継いで発展させたのが、ルドヴィンカの親友のフェルディナント・ポルシェで、それが有名なフォルクスワーゲン・タイプ1(ビートル)である。ビートルはリヤエンジンのため、トルクチューブは不要で、フロアパネル+鋼管チューブにフレームの役割を与えている。
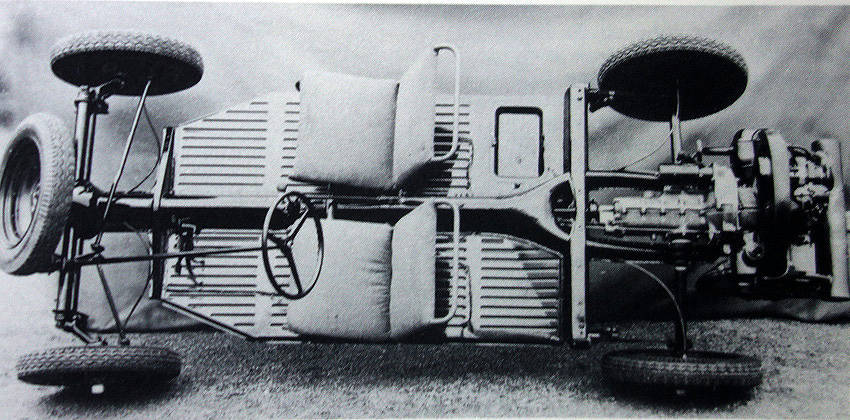
したがってビートルはアッパーボディなしでもフロアパネルにエンジンやサスペンションを装着すれば走ることができるわけだが、特徴的なアッパーボディはすべてスチールで作られ、フォロアパネルに溶接されていた。
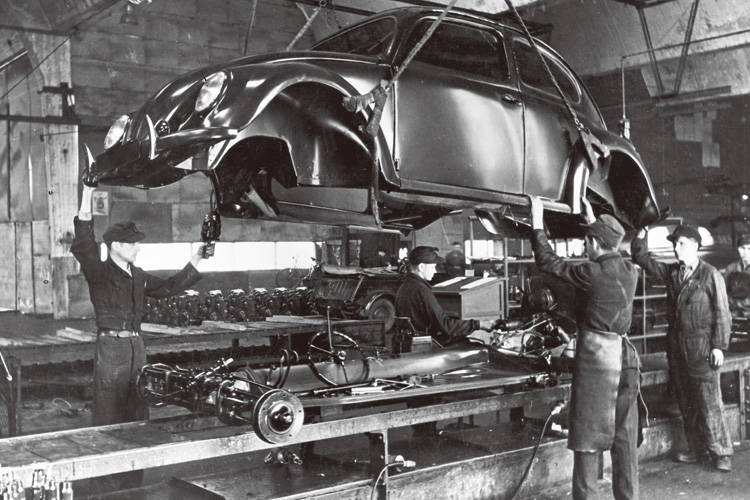
この結果、アッパーボディも荷重を負担するモノコック構造となっていたわけだ。そのアッパーボディのパネル部が荷重、路面入力を負担するという発想は、じつは航空機のモノコック・ボディから着想を得ている。
まさにボディ構造の革新である。一方、ベンツを始め、他のクルマは戦後になってオール金属のアッパーボディを採用したものの、ベースのフレームはX字型などのフレーム構造を守っていた。
1960年代に入って、乗用車はオール金属ボディとなり、従来のフレーム構造式から、ユニット構造へと変化する。ユニット構造は、モノコック構造の発展型で、フロアパネル、アッパーボディの骨格、アッパーボディのパネル部などクルマの機能に合わせたスチール材を溶接で結合する構造だ。この段階で、フロアパネルはプラットフォームと呼ばれ、プラットフォームとボディの骨格部が溶接結合され、荷重、入力を負担する構造になった。
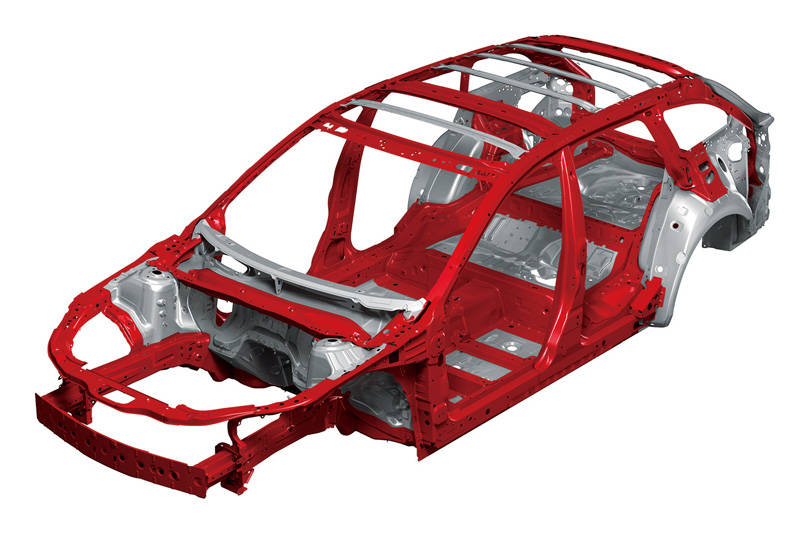
このユニット構造は、各ボディ部品がすべてプレスで成形され、溶接で結合するため大量生産にも向いていた。つまり、フォルクスワーゲン・ビートルのボディ構造を発展させたものとも言うことができるわけだ。
■現在のクルマのボディ
現在では、ヘビーデューティ4WD車、大型トラック、バスなどは依然としてラダー式フレーム構造を守っているが、乗用車はすべてユニット構造を採用している。しかし、ユニット構造にはなっても、ボディに関しては依然として強度や耐久性の指標はあったが、今日でいう剛性、ねじれや曲がりに関する指標はなかったので、各自動車メーカーが経験に従ったボディ作りを行なっている。
その原因は、ユニット構造では多くのボディ部品を組み合わせ、溶接して結合するため、そもそも剛性を測ることが困難だったからだ。
しかし1970年代後半からアメリカで衝突安全性がクローズアップされ、各自動車メーカーは否応なくボディの強化が求められるようになった。キャビンが衝突時に変形して乗員を損傷させることがないように、キャビン部分の骨格の強度は高められ、またキャビンの前後は衝突時に変形しながら衝撃を吸収することが求められるようになった。
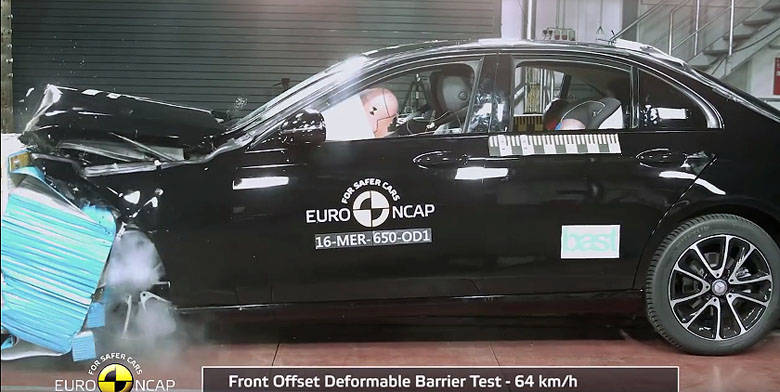
もうひとつの観点は、操縦安定性や乗り心地の向上という課題である。エンジンの出力が時代とともに大きくなり、車両重量も増大。さらにタイヤの扁平化が進みタイヤ自体のグリップ性能も年々高まった。
その結果、操縦安定性や乗り心地に関わるサスペンションの動きが改めて検討された結果、サスペンションそのものをいくら改良しても、ボディ側をしっかりさせないと狙い通りの性能が実現できないことが明らかになった。1980年代半ば以降には、部分剛性、局部剛性という用語が登場している。これは、サスペンションの取り付け部の剛性を高めないとサスペンション本来の性能が実現できないことが明らかになったことを意味している。
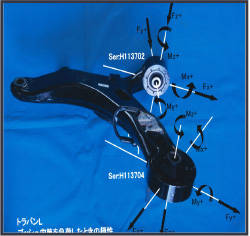
そのため、クルマの開発中にサスペンション取り付け部にさまざまな補強をして、その効果を実走行で確かめるという作業が行なわれることが当たり前の風景になった。
■ボディはさらに進化する
ボディの構造に大きな影響を与えたのは衝突安全性の規制強化であり、各地域で公的機関による衝突実験とその評価が発表される。アメリカでは1979年からNCAP(New Car Assessment Program)が開始され、日本では1995年、ヨーロッパでは1997年からNCAPが実施され、ボディ全体の強化は進んだ。だが、その反面、車両重量は増大した。
またもう一方で、燃費の向上、排出されるCO2の削減もクルマに求められるようになった。そのためにはエンジンの改良だけではなく、車両重量の低減も必須課題になってくるのだ。
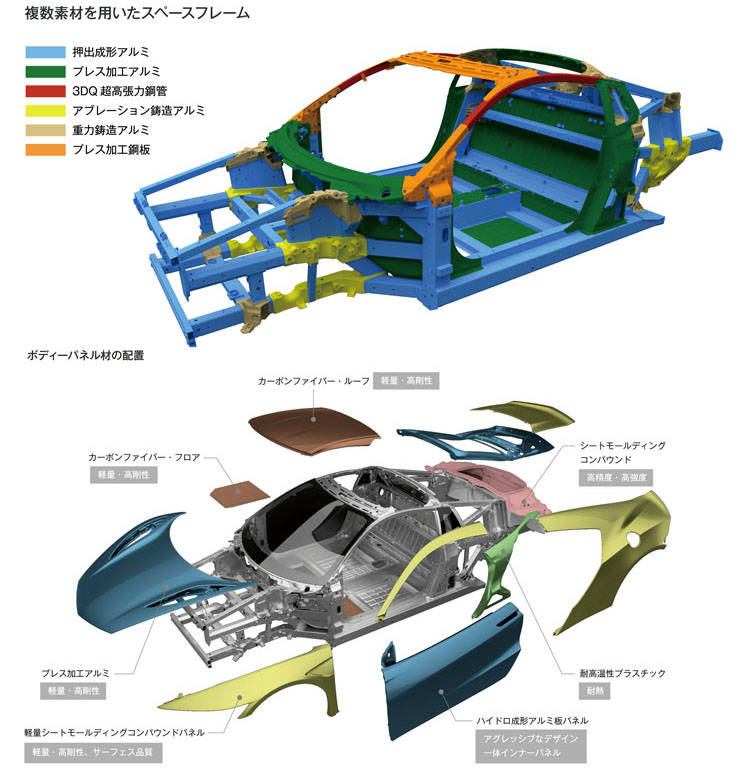
クルマの強度の絶え間のない向上と、軽量化を両立させるためには、ボディの構造を見直すとともに、ボディ素材の革新が訪れることになる。ひとつは材料置換で、アルミ材をボディ・パネルに使用したり、ボディ骨格にも採用するトレンドが生まれた。ただしアルミ材はスチール材より高価なため、ボディ骨格にまで使用するのは高級車に限定されている。
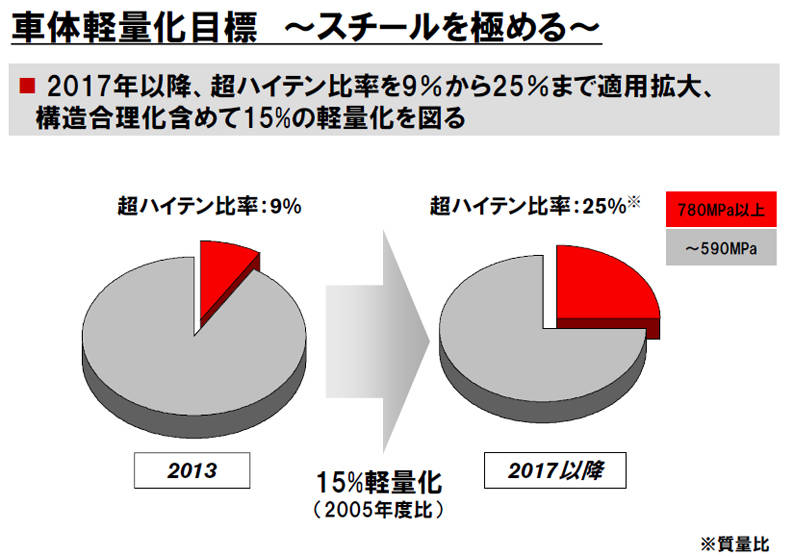
大量生産を行ない、コストの制約も大きなクルマに投入されたのが高張力鋼板、超高張力鋼板だ。もちろんこれらは製鉄メーカーが開発したもので、本来は高い強度が求められる構造用材料として開発されたが、自動車メーカー用の薄板鋼板より高い強度、靭性を持つ高張力鋼板が登場した。
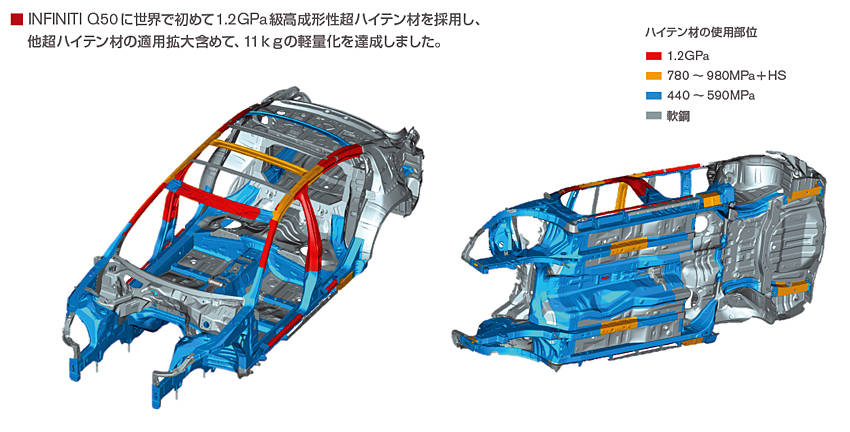
これらは普通鋼板より高強度のため、従来と同等レベルの強度であれば、より薄い鋼板を使用することができ、それだけ軽量化に繋がる。またより高い強度が求められる部分には従来の普通鋼板と同じ厚みで使用する。
この結果、ボディの軽量化も実現できるようになっている。ただ、衝突安全性の向上、さらなる軽量化の動きは止まることがないので、高張力鋼板から一段高い強度を持つ超高張力鋼板も登場している。
ただし、超高張力鋼板のレベルになると、従来のようにプレス機で加工する手法も困難になる。そのため、ホットスタンプと呼ばれる、加熱しながら成形加工し、その後に急冷する方法や、プレス機に適合できる冷間加工が可能な超高張力鋼板も登場している。ホットスタンプはヨーロッパ系の自動車メーカーが多用し、日本では冷間プレス式の超高張力鋼板が主流になっている。
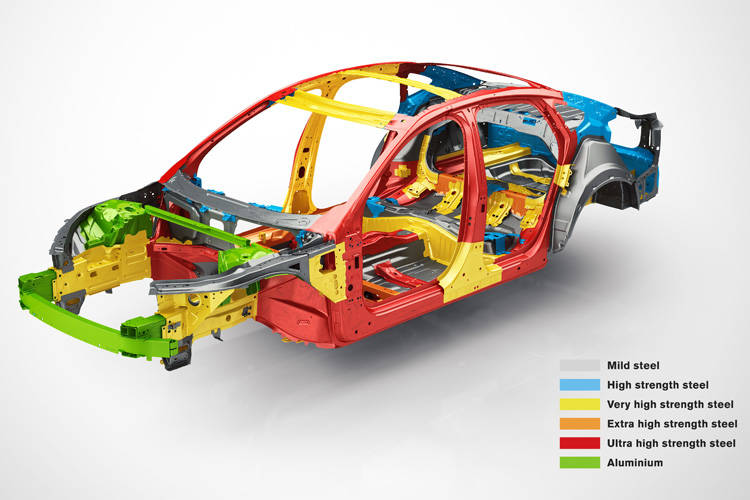
ホットスタンプは、専用の大掛かりな工場設備が必要になるが、日本ではこれを嫌い、冷間プレス式が主流だ。ただし、冷間加工とはいえ、材料の硬さ、バネ特性が強いので、一般的なプレスでは対応できず、専用の金型やプレス技術が要求される。
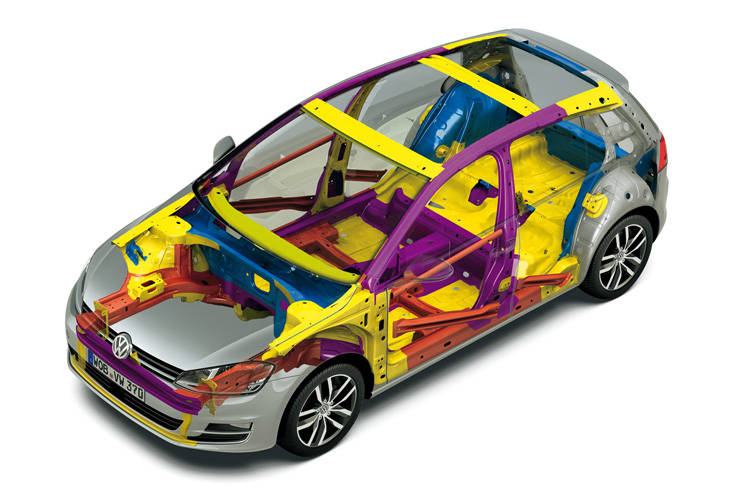
ボディの製法では、剛性を高めるため従来のロボットによるスポット溶接一本槍から、線で溶接するレーザー溶接、構造用接着剤の併用なども普及しつつある。ただし、レーザー溶接はスポット溶接より溶接時間が長くなるため、日本ではほとんど普及していない。
トヨタは、レーザースクリュー溶接という新たなにレーザーによる点溶接が可能になっている。また接着剤の使用は、工場内での設備や、接着剤の取扱性の悪さから工場では敬遠されてきたが、近年は採用車種が大幅に増加している。
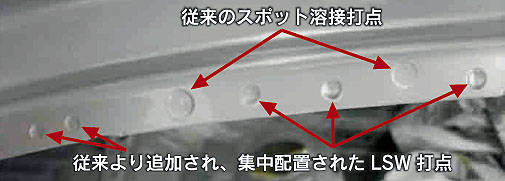
また、スポット溶接をできるだけボディ骨格の内側にもできるようにするため、インナーフレーム構造を採用する日本車も登場した。このインナーフレーム構造は、もともとヨーロッパ車が採用していた技術で、ボディの骨格部を先に溶接で組み上げ、最後にアウターパネルを溶接するという手法だ。
この場合、骨格部を先に入念に溶接できるため、強度が必要な骨格部分にスポット溶接を十分に行ない、最後に強度へ影響の少ないアウターパネルを溶接することで、軽量かつ強度・剛性の高いボディを作ることができる。日本ではホンダがN-BOXシリーズで初採用し、その後は各車種に展開している。ただし、この組立構造を実現するためには骨格部、アウターパネル部の溶接時の位置合わせの精度を高める必要があり、それなりに専用の設備が必要になる。
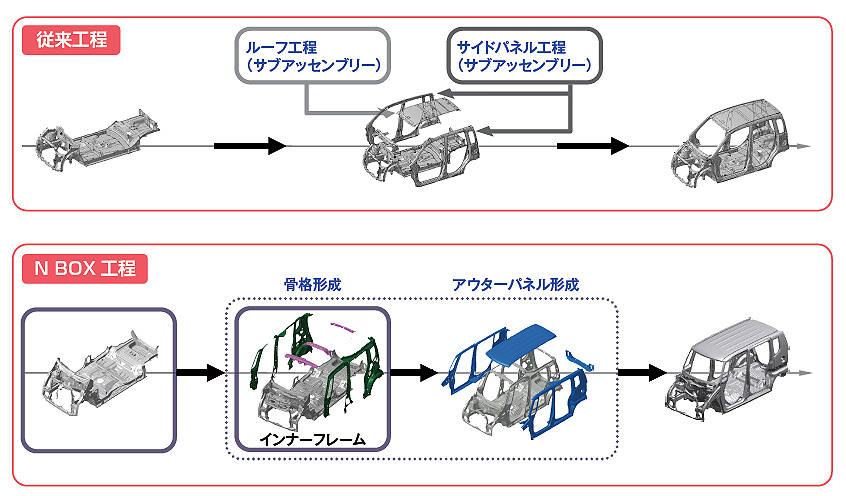
クルマを製造するためにはボディの素材となるスチール材をプレス加工し、溶接して組み立てるというきわめて大掛かりな設備が必要で、自動車メーカーはこうした工場設備を刷新するには抵抗が大きい傾向があった。しかし現在では新世代プラットフォームの導入、新たな組み立て用の技術の導入なしには、さらなるボディの衝突安全性向上や軽量化は難しくなってきている。
そのため、フォルクスワーゲンのMQB戦略、トヨタのTNGAの導入など、世界ナンバーワンを争う大量生産メーカーもボディ作りの革新を行なうために、巨額な設備投資を行ない、大規模な生産設備の更新を進めている。
ある自動車メーカーのエンジニアは、「今ではサスペンションもトランスミッションも、場合によってはエンジンも他社から購入できるが、ボディだけはどんな自動車メーカーでも自分の手で作らなければならない。だからボディ作りはその自動車メーカーの実力を示し、クルマの性能は結局ボディの良し悪しで決まる」と語っているが、まさに目には見えないボディの性能こそクルマの性能と言ってよいだろう。