日産自動車は2019年10月2日、金型を使用しないでボディパネルを成形する「対向式ダイレス成形」技術を開発し、実用化したことを発表した。この技術を活用して、日産はアフタ―サービス部品や、すでに金型のない旧型車の補修部品の商品化を想定している。
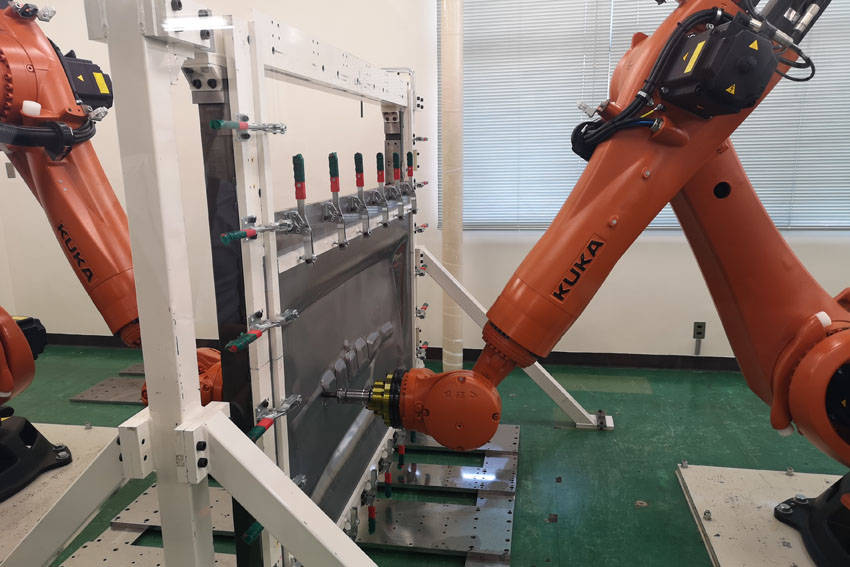
技術概要
今回発表されたのは、すでに金型もない旧型車のパネルや、カスタマイズカー向けなど、少量生産を前提としたパネル成形の新技術だ。
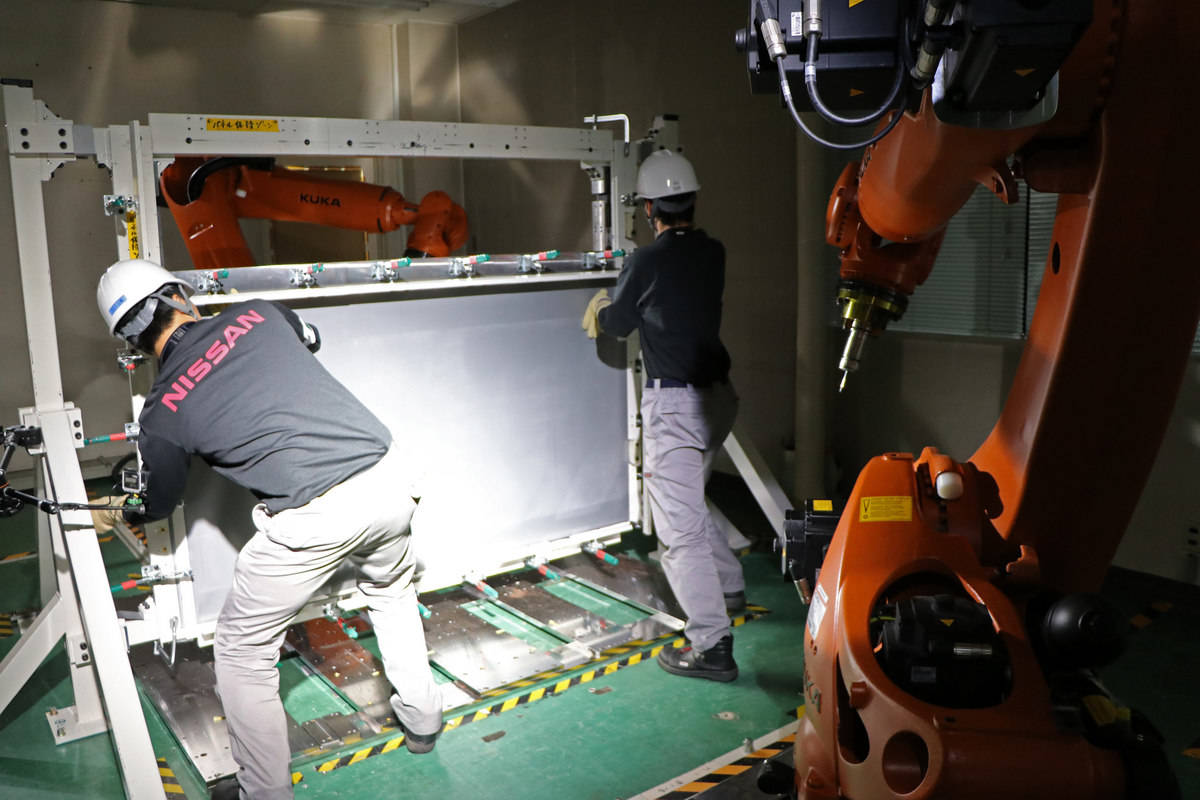
量産車のボディパネルは巨大なプレス機と、重さ数トンの金型を使用してプレス成形されるが、金型費の開発や時間、プレス機の準備期間がかかるなどの理由で少量生産には不向きだ。そのため、少量生産向けのパネル成形技術としてインクリメンタル成形がある。インクリメンタル成形とはNC加工機などを使用して金型なしで逐次に伸展加工する方法だ。
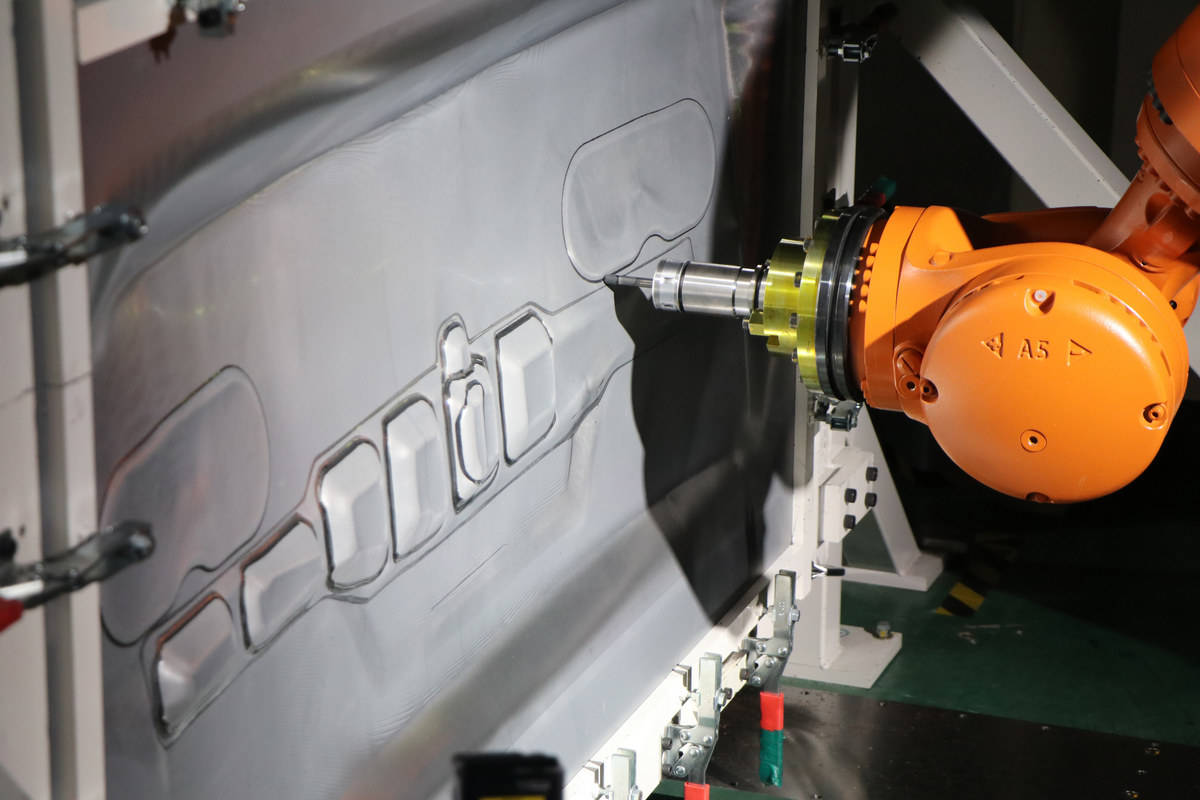
ただしNC加工機によるインクリメンタル成形は、加工するパネルサイズに制約があるなどの問題があった。そこで日産は、汎用のロボットを2基使用して、1枚のパネルを両方向から加工する「対向式ダイレス(金型レス)成形」を開発した。
2基のロボットに棒状の専用工具を取り付け、両側からパネルを徐々に変形させて成形し、より複雑な形状の高精度な成形も可能にしている。
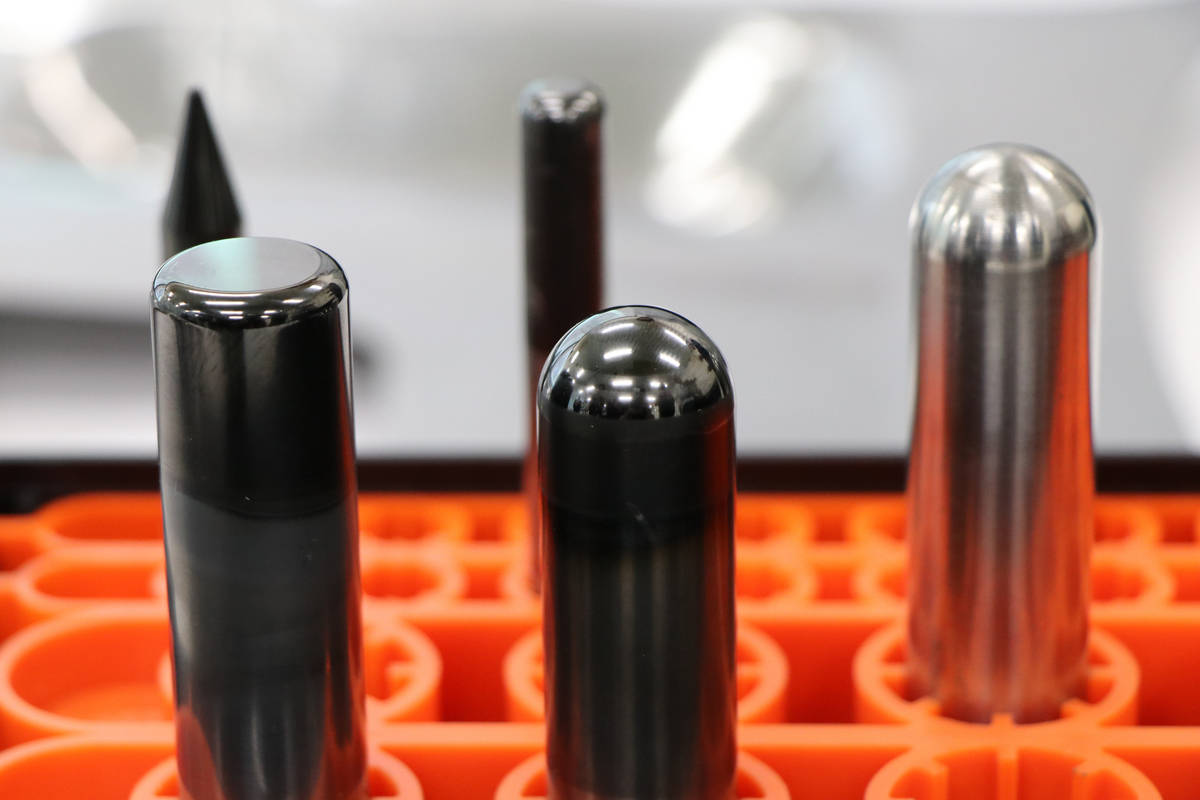
ただ、従来は対向するロボットの工具を連携させながら成形する工法は、2つのロボットの制御が難しく、これまで実用化は困難とされてきた。また従来の工具では整形したパネル面が粗くなり、そのままでは塗装ができないという問題もあった。
生産技術研究開発センターがこの対向式加工の制御プログラムを開発し、総合研究所の工具材料の研究により工具の加工部をダイヤモンド・ライク・コーティング(DLC)し、鏡面状態にすることで実用化に成功した。パネルを成形加工する工具が鏡面状態のため、低摩擦で加工時の潤滑も不要だ。
ロボットの制御プログラムは、パネル材のスプリングバック(加工後のもどり変形)なども考慮し、工具ロボットの最適軌道生成ロジックなどを盛り込んでいる。
今回は、要望の多い旧型スカイラインのリヤ・パネルなどの加工や、成形された完成品のパネルが披露された。現在は、純正部品化に向け、検討を行なっているという。