この記事は2018年1月に掲載した有料記事です。
■軽量化という課題
クルマの電動化の動きが世界的に加速しているが、ハイブリッド→PHEV→電気自動車になるにつれて車両重量はどんどん重くなる。その理由はバッテリーの容量に比例して重量は大きくなるからだ。
100kWhの大容量バッテリーを搭載するテスラ モデルS P85Dのボディはアルミを多用した軽量構造になっているが、車両重量は2100kgと相当に重い。原因は巨大なバッテリー重量のためだ。
電気自動車の電費を向上させ航続距離を伸ばすためには、空力性能の向上と同時に、ボディ全体の軽量化を行なうことは重要な課題になっている。もちろん内燃エンジン車にとってもボディの軽量化は燃費を低減し、CO2排出量を削減するためにきわめて有効だ。どれだけエンジン技術を革新しても、ボディ重量が重くては燃費の改善は微々たるものに過ぎない。
また、そもそもクルマの走る、曲がる、止まるという基本性能を高めるためにはクルマの重量は軽いほど有利であることはいうまでもない。
時間を少し巻き戻してみると、時代とともにクルマのサイズは大型化し、車内装備も充実化されクルマの重量は増加した。例えば1950年代半ばの「メルセデス・ベンツ 220S(現在のSクラスの原点モデル)」の車両重量は1350kgであったが、現在のSクラスの最も軽量なモデル「S400」でも車両重量は1950kg、「S560 4-MATICロング」では2220kgになっている。
また1980年代以降は、衝突安全性を高める社会的な要請が高まり、衝突安全性能を向上させるために強度、剛性の高いボディが追求された。その結果、クルマの重量は増大の一途を辿ってきた。
こうした時代とともに増大したクルマの重量の増大傾向に歯止めをかけ、逆に軽量化方向に向かうきっかけとなったのは、やはり燃費の低減、排出ガスの削減という大きな社会問題がクルマに突き詰められたからだ。
衝突安全性能をより向上させ、同時にクルマ全体の重量を低減するという、いわば二律背反の課題を解決することが自動車メーカーにとって重要な技術テーマになったのだ。特に今後の電気駆動化の時代を迎え、大容量のバッテリーを搭載する場合は、その重量増大をどのようにカバーして軽量化を行なうのか?ということは大きな課題なのである。
■高張力鋼板
クルマのボディを軽量化するためには、大別して構造の合理化、工法の改良、そして材料置換という手段が存在する。構造をよりシンプルにし、補強材などを不要にする。そして工法を一新することでボディ結合などでの贅肉を削減して、高張力鋼板、アルミ材や樹脂材、カーボン材など、より軽量な材料に置き換えるといった手法が知られている。
しかし、アルミ材やカーボン材を多用すれば当然ながらコストが上昇するので、車種に合わせて最適なコストのもとで軽量化を進めることが重要なポイントになっている。
大量生産されるクルマで軽量化を進めるために、現在一般化しつつあるのが高張力鋼板の採用拡大だ。高張力鋼板は、「ハイテン」(High Tensile Strength Steel Sheets)とも呼ばれる引っ張り強さが高い薄板鋼板のことである。普通の薄板の鋼板が引っ張り強さは270MPa以上といったレベルに対して高張力鋼板は340MPa~790MPaという強度を持つと定義されている。
ただし、この定義は各国によって多少違っているが、490MPa以上を高張力鋼とする見解も多い。また引っ張り強さ980MPa以上の鋼板は現在では「超高張力鋼板」(スーパーハイテン)、1000MPa(1GPa)以上は超々高張力鋼板と呼ばれている。
高張力鋼板の種類には,炭素の他にニッケル、シリコン、マンガンなどの元素を添加して強化した鋼板、プレス成形後に焼入れして強化した複合組織鋼板などがある。またプレス成形する前に材料を加熱して、成形後急冷して強度を高める熱間プレス成形法(ホットスタンプ)が開発され、複雑な形状の、しかも1GPa以上の強度を持つ超々高張力鋼板も採用されるようになっている。
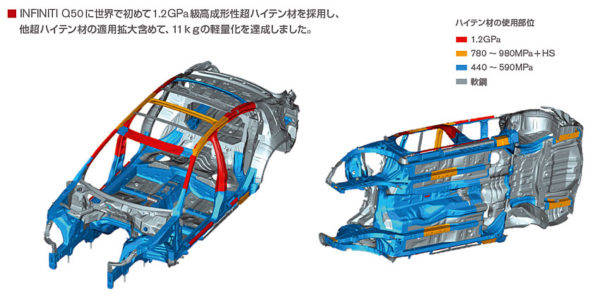
また近年は、ホットスタンプではなく冷間プレスに適合する1GPaクラスの超々高張力鋼板も登場している。高張力鋼板の強度を上げるほど成形性、つまりプレス加工が難しくなることが課題であったが、材料の改良、プレス技術の改良により実現している。この冷間プレス可能な超々高張力鋼板は、ホットスタンプ加工より設備投資が少ないことがメリットになる。
しかし、次世代のホットスタンプでは2GPaクラスを目指しており、このクラスになると割れにくく、粘りのあるホットスタンプが有利とされている。
現在のクルマの外板パネルは340MPa級が採用され、メンバーやピラーなどの構造部材では440~980MPa級の高張力鋼板の採用が進んできている。さらにバンパーや側突対応のAピラー、Bピラー内部には980MPa~1.3GPaの超高張力鋼板も使われ始めている。
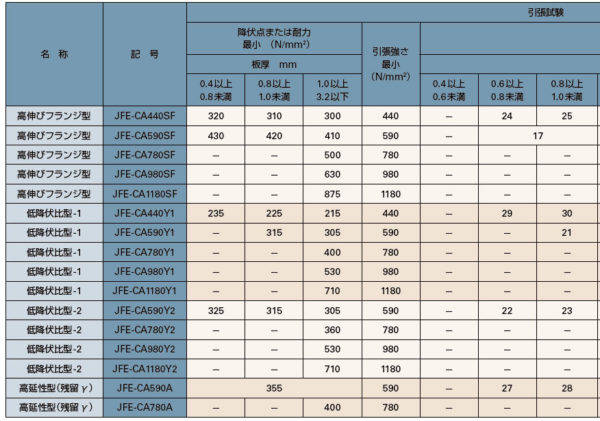
こうした高張力鋼板は従来の鋼板より強度が高いため、普通鋼板と同等の強度にするためには薄板化が可能で、薄くなった分だけ軽量化が実現するのだ。ただし、薄板化により剛性も低下しやすいので、その対策を行なったり、さらに強度を高めるといった使用法が主流だ。そのため、超々高張力鋼板と高張力鋼板を組み合わせるなど材料の特性と使用場所に合わせた設計手法が求められている。
■アルミ材
アルミは35%の比重で、軽量な素材だ。加工もし易い特長があるが、自動車用に使用するためには使用部位に合わせて強度や剛性を確保する必要があり、鉄部品をアルミに置き換えたとしても重量は1/3にはならないのが実情だ。だが、パネル部分はもっとも採用しやすい場所で、軽量化にも貢献する。アルミ材は材料そのものや加工のコストが鋼板より高いのもネックになっている。
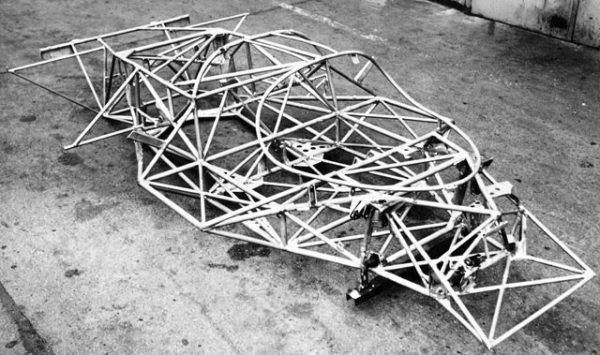
戦前から1960年代までのレーシングカーは細い鋼管製のスペースフレームにアルミパネルを張った構造が主流であり、1969~70年代にル・マン24時間レースやマニュファクチャラーズ選手権で活躍したポルシェ917はアルミパイプによるスペースフレーム構造を採用し、フレーム重量は50kgを切るほどの軽量さを誇った。
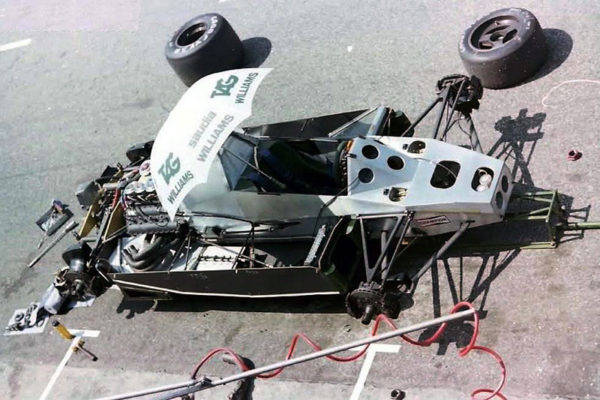
このように、初期のアルミ材はパネル、またはアルミ・パイプが使用された。その後のレーシングカーはアルミパネル材をボックス形状にし、内部に構造材を組み合わせたバスタブ型モノコックが主流になったが、後述するが、1990年代以降はカーボン製のモノコック・フレームに切り替わっていった。
市販車では、スーパーカーがいち早くアルミパネル材を採用している。量産乗用車としては1994年にデビューしたアウディA8がASF(アウディ・スペース・フレーム)のコンセプトのもとでオール・アルミ製のボディを実現している。ASFはスペースフレームという名称を使用しているが、アルミ製の骨格とアルミパネルを組み合わせた現代的な構造となっている。
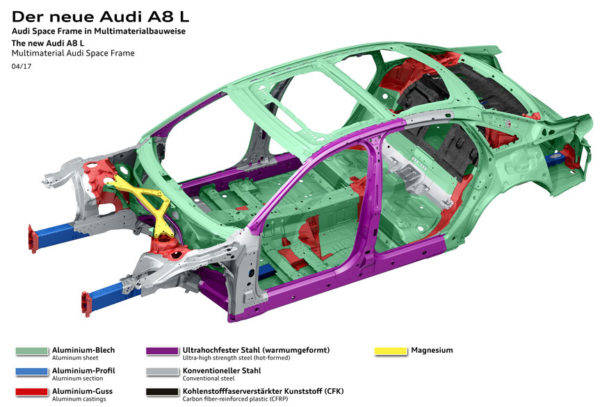
アウディはその後も軽量構造の追求を継続し、現在ではアルミを主要骨格とした超々高張力鋼板、アルミパネル、カーボン材などを組み合わせたマルチ・マテリアル・スペースフレームとしており、A8だけではなく他の車種にも拡大採用している。

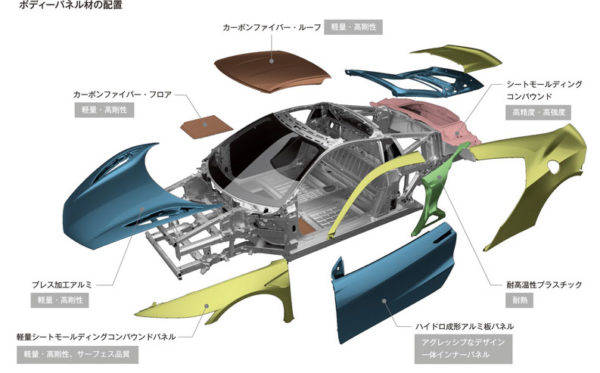
現在では、プレミアムクラスのクルマはボンネットやトランクリッド、ドア、フロント・フェンダーなどにアルミ材が採用されている他に、サスペンション、サブフレームなどにもアルミ鍛造材や鋳造材が使用されている。
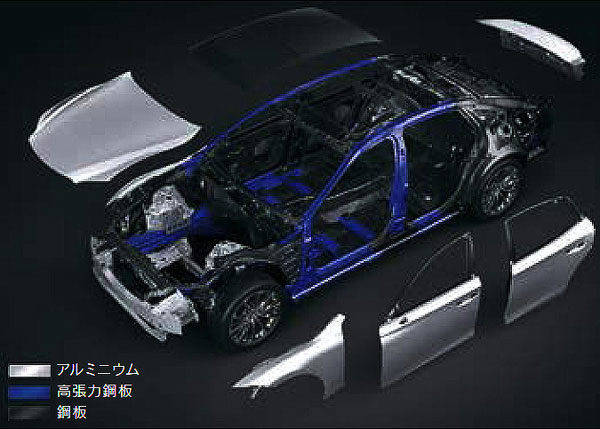
■カーボン、プラスチック材
現在のレーシングカーはモノコック&シャシー、ボディパネルはすべてカーボン(CFRP)材で作られている。カーボン材は鉄と比べて比重が1/4、比強度が10倍、比弾性率が7倍と優れた物性を備えており、金属を超える材料と位置付けられている。
しかし、レーシングカーのカーボン材(炭素繊維強化プラスチック)はプリプレグと呼ばれる樹脂を含浸させたカーボン繊維を型に合わせて何層か貼り合わせて成形する手作業が必要で、さらに成形後に電気オーブン(オートクレーブ)で加熱硬化させるタイプのため、成形には熟練工による長い作業時間が必要になる、単品生産は可能だが乗用車のような量産化はきわめて困難とされてきた。
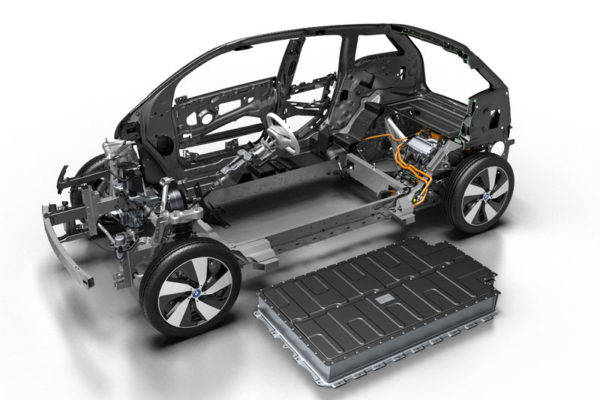
そのためCFRPは自動車用より先に航空機用、産業用の素材としてさまざまな成形法が開発され、その過程で、自動車のボディ用として使用できる可能性が高まってきた。量産に適した製法としては、RTM(レジン・トランスファー・モールディング)、プリプレグ・カーボンシートを使用するPCM(プリプレグ・コンプレッション・モールディング)などが登場した。
PCMは、積層したプリプレグ材をプレス機で圧縮成形し、約5分のサイクルタイムで、部材の量産を可能としているので、自動車用の部品として使用できるようになっている。
各自動車メーカーもCFRPの研究を行なっているが、いち早く量産技術として確立させたのがBMWである。電気自動車のi3、PHEVのi8を開発するにあたり、ボディの軽量化を徹底的に追求し、カーボン材による骨格構造を開発し、実現した。
BMWは量産化を可能にするため、従来のプリプレグ・カーボン方式ではなく金型に熱硬化樹脂とカーボン繊維を入れて加熱するRTM(レジン・トランスファー・モールディング)を採用した。なおBMW社が使用する炭素繊維は三菱レーヨン製、繊維加工はドイツのSGL社が担当している。SGL社はBMWと同資本系列の企業のため、カーボン製品化が迅速に実行できたという背景もあるようだ。
これにより従来のカーボン材の成形の課題を大幅に解決し、もちろんまだ製造コストが高いとはいえ量産車への適合が実現している。この結果、同様のボディサイズのフォルクスワーゲン eゴルフの車両重量が1590kgに対して、eゴルフよりややバッテリー重量の重いBMW i3の車両重量は1300kgときわめて軽量に仕上がっており、カーボン・フレームによる軽量化の効果がわかる。
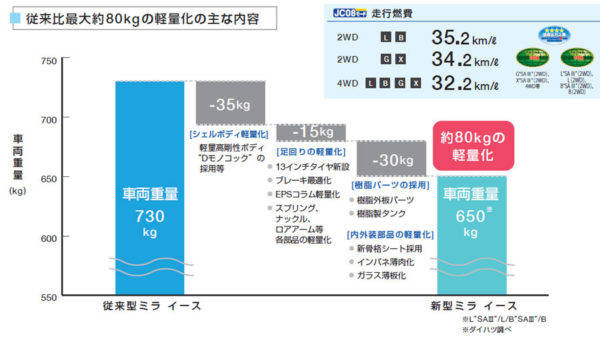
また、カーボン材とは別に、量産車のパネル部分に使用するSMC樹脂の開発、実用化も進んでいる。ダイハツの軽自動車に多用されるSMC(シート・モールディング・コンパウンド:ガラス繊維樹脂)も注目される。SMCは低圧での加熱成形により大量生産が可能で、ローコストでありこの素材の使用も軽量化の手法として有効だ。
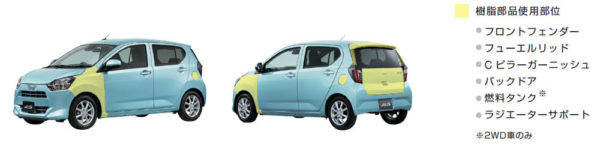
自動車の大幅な軽量化という課題に対して、スチール、アルミ、カーボン材、SMC樹脂とそれぞれの素材を使いこなす技術の競争はこれからより激化すると予想される。軽量化は、目に見えないある意味で地味な技術だが、クルマの性能を本質的に高めることができる重要な技術なのである。